Time to revise or replace your PLC? Use the decision tree
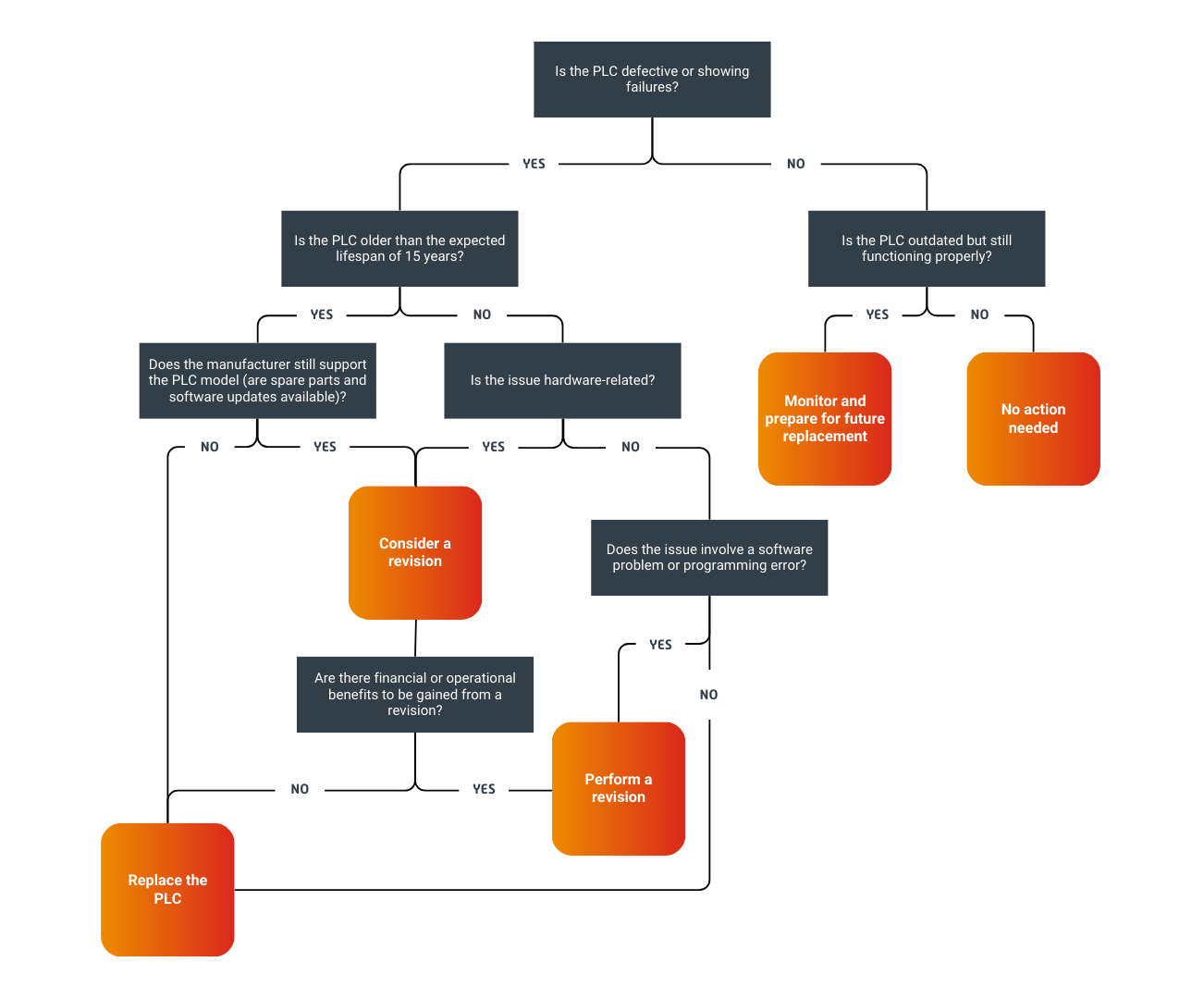
A Programmable Logic Controller (PLC) is a crucial component of many industrial processes. However, like any technology, a PLC has a lifespan, and sooner or later, the question arises: should we revise or replace it? The decision tree above can help guide you in making this choice.
When is it time to take a closer look at your PLC?
A PLC can function reliably for many years, but failures or technological obsolescence may occur. The first step in the decision tree is to determine whether the PLC is defective or experiencing failures. Failures can range from minor glitches to serious problems that disrupt production. Sometimes these failures can be fixed with minor adjustments, but in other cases, more in-depth investigation is required.
If the PLC is still functioning well but is outdated, it’s advisable to monitor the situation. Although no immediate action is needed, it’s wise to start preparing for a future replacement. This prevents unexpected downtime and ensures you can select a suitable replacement in time.
If the PLC is no longer functioning properly, it’s necessary to investigate whether the issue is hardware-related or software-related. This helps determine the next step in the process.
Revise or replace: what is the best choice?
When a PLC shows problems, the age of the system is an important factor. The average lifespan of a PLC is about 15 years. After this period, the likelihood of failures increases, and spare parts and software updates can become harder to find. If the manufacturer still offers support for the model, a revision might be a good solution. This may involve replacing components or updating the software to improve functionality.
If the manufacturer no longer offers support and spare parts are unavailable, replacing the PLC is often the best choice. This prevents future issues and ensures that the system stays up-to-date with the latest technologies.
Another important consideration is whether the issue is hardware-related. Hardware problems can range from defective components to outdated wiring. In some cases, a revision may resolve the issues, especially if there are financial or operational benefits. However, if a revision offers no significant advantages and the likelihood of recurring failures is high, replacement is the better option.
For software-related problems or programming errors, revision is often the most logical solution. This can involve optimizing the code, fixing errors, or adding new features to improve efficiency. A software update can extend the life of the PLC without the need for a full replacement.
Conclusion
By following this decision tree, you can make an informed choice regarding the maintenance or replacement of your PLC. Regular monitoring and timely revisions can extend its lifespan and prevent unexpected downtime. It’s always advisable to consult a specialist if you’re unsure about the best choice for your situation. This way, you can ensure your production process continues to run smoothly and avoid unplanned downtime.
Stay up-to-date
Receive the newsletter in your inbox every month.
Or follow us
Share this article
Others also viewed
What should you consider when choosing a SCADA/MES system?
A good SCADA/MES system plays a crucial role in this. It enables companies to collect production data, monitor processes, and intervene immediately in case of failures or deviations. However, not every system…
7 reasons why users love Ignition
Imagine always having a reliable partner who not only stands by your side when you need them, but also helps you grow and overcome every obstacle. Sounds like the perfect match, right? That’s how it feels with Ignition.
Stay smart, connected, and secure in a modern production environment
In a world increasingly reliant on digital and connected technologies, production environments face risks. However, this doesn’t mean you have to choose between progress and security.