» What is a DCS?
» How does it work?
» Who uses it?
» What are the advantages of a DCS?
» What are the differences with a PLC?
» The difference between a DCS and an RTU
» What is the difference between DCS and SCADA?
» Ready to master your growth?
Other knowledge base articles
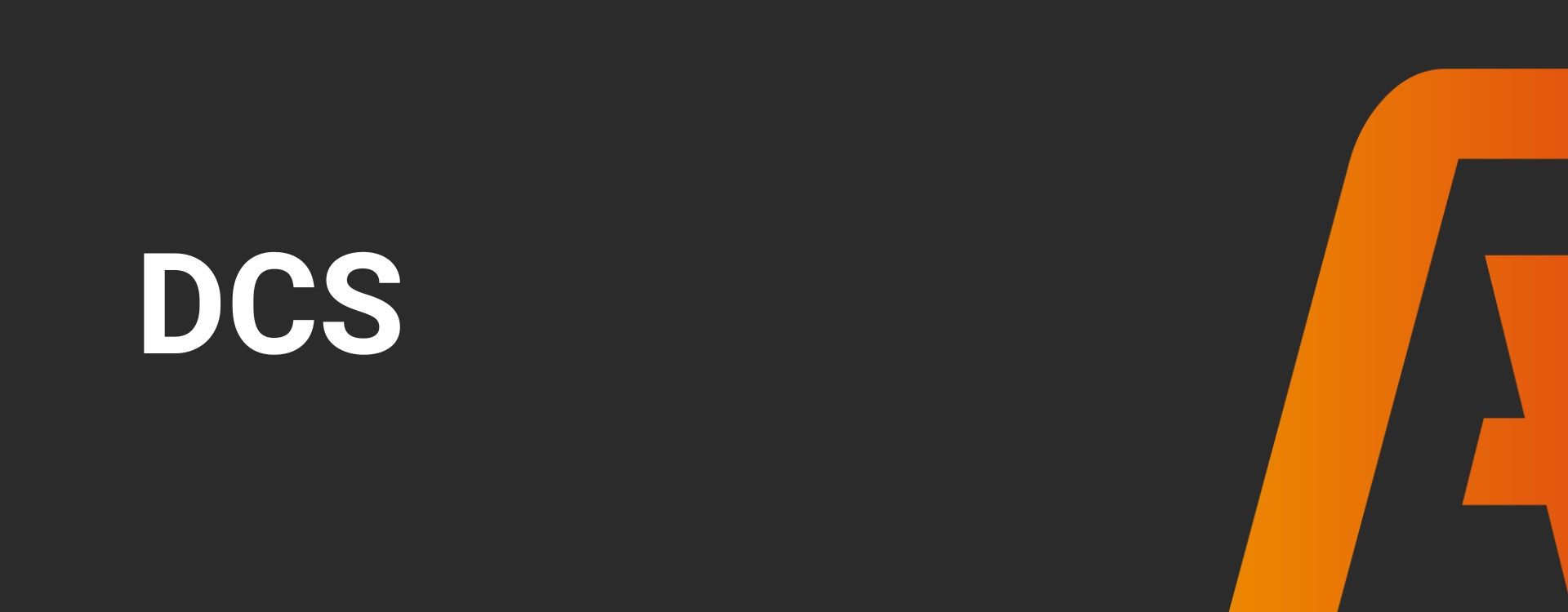
DCS
What is a DCS?
A DCS stands for Distributed Control System. It is a type of industrial control system used for the monitoring and control of industrial processes, such as those in factories.
This system features a central control room from which operators monitor and control the process. Additionally, it consists of a network of external field devices such as sensors, actuators, and control valves spread throughout the process.
The system operates using a distributed architecture, where the control logic is distributed across multiple controllers rather than being centralized in one controller. This provides increased flexibility and scalability, as well as the ability to control and monitor processes in real-time.
DCS systems are more robust than other control systems. They continue to operate even if a controller or field device fails, enabling a higher level of availability and reliability. They are highly adaptable and designed to meet the specific needs of a particular process.
How does it work?
A typical DCS system consists of several main components:
- Control processors: These form the “brain” of the system. They are responsible for executing the control logic and making decisions based on process data. They operate both hardware and software.
- Input/Output modules: These I/O modules serve as interfaces with field devices such as sensors and actuators. They are responsible for collecting data from the field devices and sending control signals to them.
- Human Machine Interface: An HMI is the user interface through which operators control the process. It typically includes a monitor, keyboard, and mouse. It is used to display process data, control the process, and acknowledge alarms.
- Communication network: The network that connects all components. This enables them to communicate with each other and exchange data.
The DCS system operates by collecting data from field devices via the I/O modules and sending it to the control processors. The control processors then use this data to make decisions and execute the control logic, such as activating a pump or adjusting motor speed based on a set of conditions. The control processors then send control signals back to the field devices via the I/O modules, which are used to control the process.
The HMI is used to display process data. Additionally, operators can communicate with the process, monitor it, and make adjustments using the HMI. They also acknowledge alarms through the HMI.
Who uses it?
DCS finds applications across various industries including chemical, petrochemical, energy, food and beverage, pharmaceutical, and water treatment industries. Companies utilize it to automate and control industrial processes and machinery, such as regulating temperature, pressure, flow, and levels of different materials.
The system is commonly found in large-scale industrial processes where various machines and components are spread over considerable distances and need to be coordinated. It is also suitable for applications requiring high reliability and accuracy, such as managing the production of pharmaceutical products.
DCS systems are often used in situations with multiple control points that need coordination, such as in a power plant where multiple operators supervise different machines and processes.
What are the advantages of a DCS?
- Centralized control: It provides a centralized view of the process and enables operators to easily monitor and control the process from a single location. This results in increased efficiency and ease of use.
- Enhanced process control: It utilizes advanced control algorithms and techniques, such as PID control and model-based control, to improve process performance and stability. This leads to greater efficiency, better product quality, and lower costs.
- Data collection and analysis: It includes capabilities for data collection and analysis, allowing real-time monitoring of the process and observation of historical trends in process data. This provides valuable insights into the process and is used to improve process performance and optimize maintenance schedules.
- Scalability: It is designed to be flexible and scalable. They are easily expandable to accommodate changes in the process and can handle a large number of devices and tags.
- Security: It incorporates various security measures to protect against unauthorized access and cyber threats.
- Cost-effective: It is cost-effective and efficient. They increase productivity, reduce downtime, and improve process efficiency, ultimately leading to cost savings.
- Alarm management: Operators are alerted to potential process issues, enabling them to take corrective action before the problem becomes critical.
- Remote access: The systems are remotely accessible, allowing operators to monitor and control the process from any location.
- Integration: The systems can be integrated with other systems such as PLC, MES, and ERP, providing more flexibility and better process control.
What are the differences with a PLC?
A DCS is designed for large-scale industrial processes and is typically used to coordinate the control of multiple processes from a central location. A DCS has a distributed architecture, where control is distributed across multiple controllers placed at different locations in the factory. The system uses advanced software and communication protocols to integrate the controllers and share data. It is suitable for applications where multiple processes, machines, and components need to be controlled and coordinated over long distances.
On the other hand, a PLC (Programmable Logic Controller) is a standalone controller typically used to automate individual machines and processes. It is a compact device that can be programmed to perform specific tasks. It is suitable for applications where control of a single machine or a small number of machines at one location is needed.
What is the difference between a DCS and an RTU?
- Function: An RTU (Remote Terminal Unit) is designed for remote data collection, local control, and forwarding data to a central control station. A DCS is designed for the control and management of complex industrial processes through the integration of hardware and software components.
- Scale: An RTU is typically used for small-scale systems, while a DCS is usually used for large-scale systems.
- System architecture: An RTU is usually based on a single controller connected to various sensors and actuators. A DCS, on the other hand, consists of multiple controllers integrated into a network and exchanging data to enable integrated control of the entire system.
- Flexibility: An RTU is relatively inflexible as it is designed to perform a specific set of functions. A DCS, however, is highly flexible and can be customized to meet the specific requirements of a particular application.
What is the difference between DCS and SCADA?
The main difference is that DCS focuses on automating and controlling processes, while SCADA (Supervisory Control and Data Acquisition) focuses on monitoring and managing processes remotely. DCS is thus more geared towards executing control functions in a process, whereas SCADA is more focused on collecting and visualizing data. However, both systems can be integrated to create a complete automation system that provides both control and visualization functions.
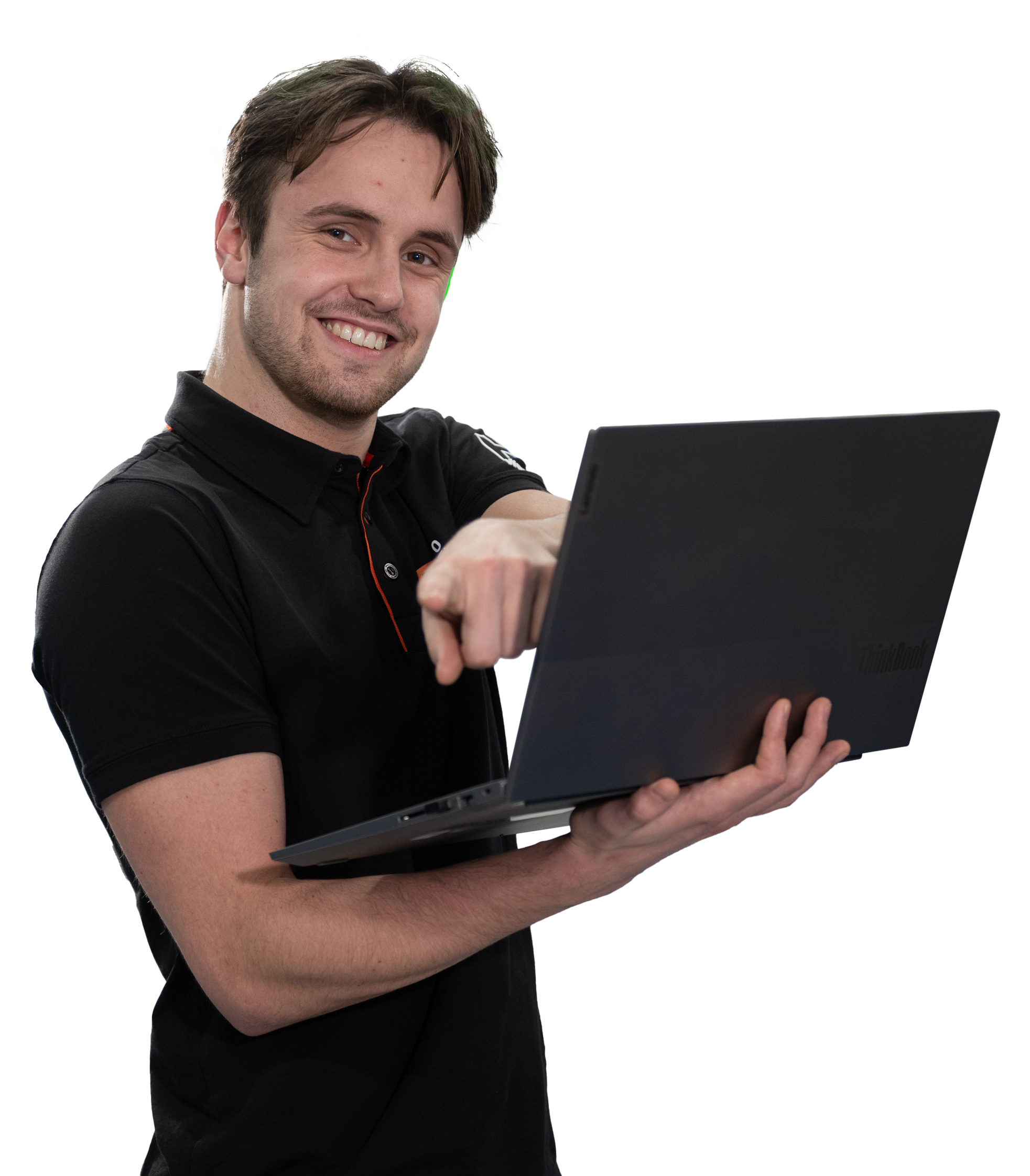
Ready to master your growth?
At AT-Automation, we aim to accelerate your growth and reach new heights of efficiency with our advanced automation solutions. We strongly believe in sharing knowledge and empowering individuals to become masters in industrial automation. Would you like free advice on how our solutions can help your business grow? Please leave your contact information below.
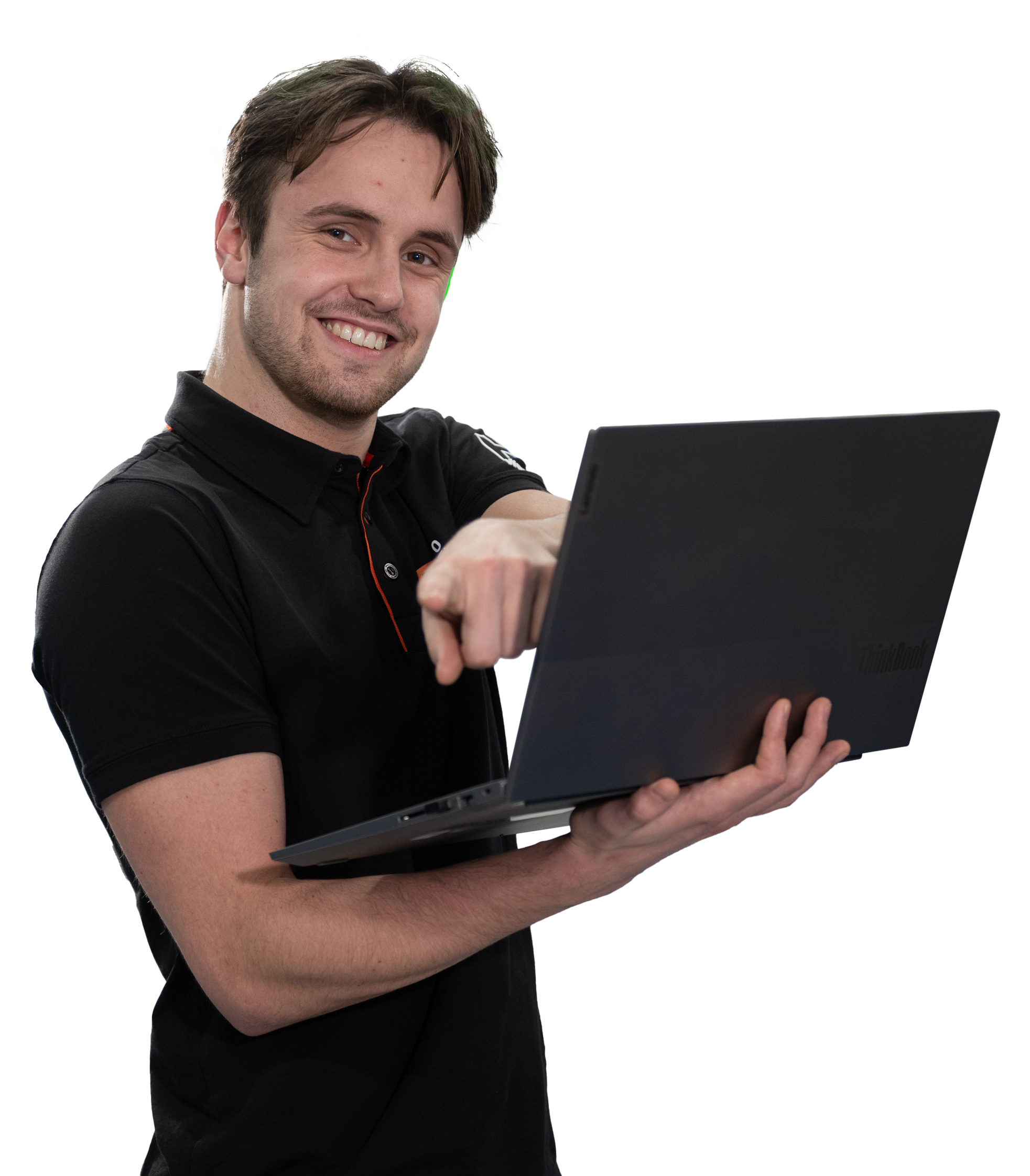