» What is an MES systeem?
» What are the key functions of an MES system?
» How does an MES system work?
» Who uses it?
» What are the benefits of an MES system?
» What is the difference with MOM?
» How does it integrate with ERP?
» MES and Ignition
» Explore Ignition
Other knowledge-base articles
» OEE
» ERP
» SPC
» Industrial Automation
» Industry 4.0
» […]
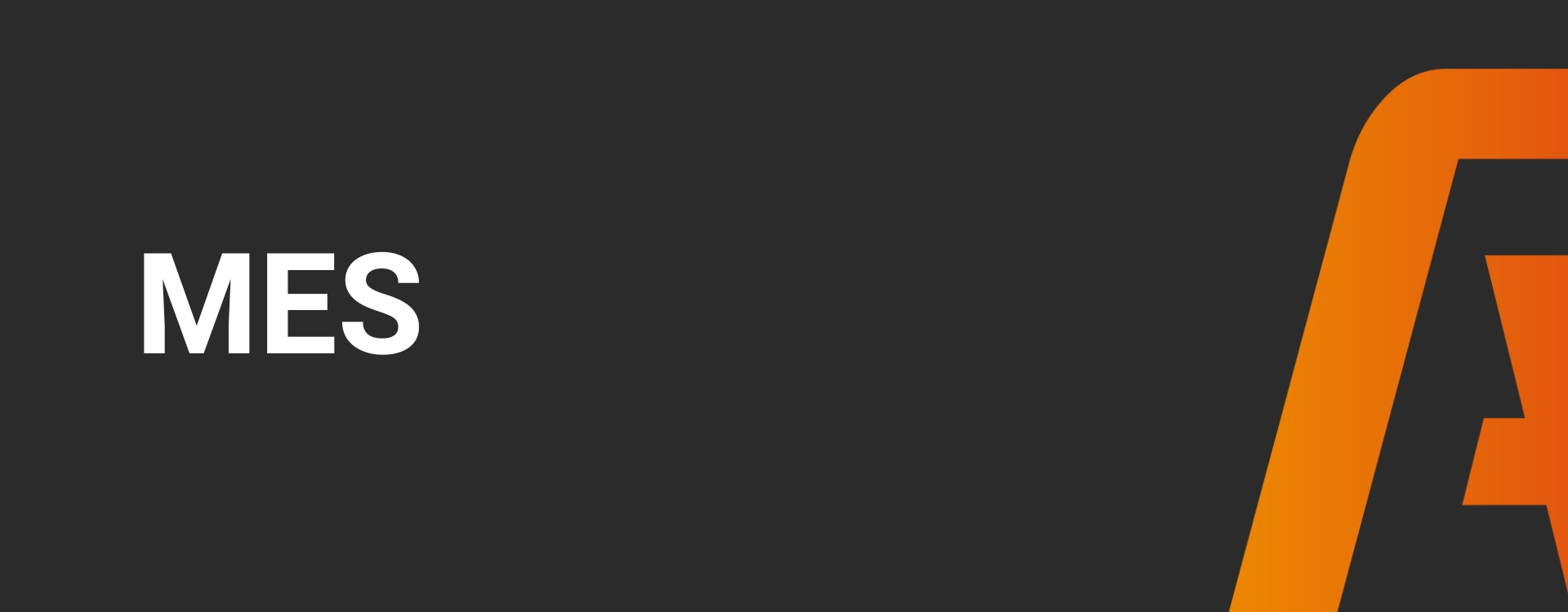
MES
What is an MES system?
MES stands for Manufacturing Execution System. This is software used to manage and optimize production processes in a factory or manufacturing company. It includes tasks such as planning, execution, monitoring, and analysis of all production activities. The goal of an MES system is to improve efficiency and productivity and quickly resolve production issues.
What are the key functions of an MES system?
A Manufacturing Execution System (MES) has several key functions related to managing and monitoring production processes. Here are some of the most important functions:
- Production planning: Plan production activities and create a production schedule based on resource availability, demand, and other factors.
- Track & Trace: Monitor and trace each product in the production line, allowing real-time tracking of its location, status, and history.
- Process control and monitoring: Monitor and control the parameters of production processes in real-time to ensure consistent production execution and compliance with standards and requirements.
- Quality control: Identify and address quality issues through real-time data collection and analysis, employing Statistical Process Control (SPC) techniques.
- Maintenance management: Manage and schedule maintenance tasks for equipment and machinery in the production line to maximize uptime and minimize costs.
- Material management: Manage inventory of raw materials, components, and semi-finished products, ensuring availability when needed.
- Reporting and analysis: Generate reports and analyses on production line performance and use them to drive improvements.
How does an MES system work?
A Manufacturing Execution System (MES) operates by collecting, analyzing, and utilizing real-time data from production processes. This data provides insights to manage and enhance the execution of these processes. The process involves the following steps:
- The system gathers data on production activities, including production orders, machine status, employee performance, and production efficiency.
- The collected data is analyzed to gain insights into the performance of production processes and to identify areas for improvement.
- The software utilizes the analysis results to plan and adjust production processes according to changing conditions.
- MES monitors the execution of production processes in real-time and makes adjustments as necessary.
- It provides reports on production performance and efficiency, aiding in the identification and implementation of improvements.
Who uses it?
These systems are primarily used by companies engaged in manufacturing processes, such as factories and production companies. They are utilized by manufacturing firms of all sizes, from small businesses to large multinational corporations, and are specifically designed to enhance the productivity and efficiency of production processes, providing insights into performance and necessary improvements.
What are the benefits of an MES system?
- Real-time insights enable companies to quickly respond to issues and make improvements in production processes, resulting in better efficiency and productivity.
- Accurate tracking and tracing of materials and products lead to improved quality control and reduction of defects and waste.
- Be more flexible and responsive by optimizing production processes and adapting them to changing requirements and conditions.
- A centralized database for production information makes it easier for teams to communicate and collaborate.
- Save (in the long term) costs by optimizing production processes and reducing waste.
- Comply with regulatory requirements regarding production processes and quality control.
- It’s easier to plan and adapt production processes to changing conditions, such as shifts in demand or machine downtime.
- Improve product quality by monitoring production efficiency and identifying improvements.
- Prevent errors in production processes by monitoring and analyzing activities and providing real-time feedback.
What is the difference with MOM?
MES and MOM (Manufacturing Operations Management) are two types of software used in the manufacturing industry, but they have different purposes and functions.
MES is focused on the execution and monitoring of production processes, such as managing production orders, tracking production progress, and monitoring production efficiency. The goal is to optimize production processes and solve production issues.
MOM, on the other hand, is a broader term that refers to managing all operational activities in a manufacturing company. This includes production, delivery, quality, maintenance, and facility management. The goal is to optimize and improve the entire operational activity of a company.
How does it integrate with ERP?
Although an MES system can be used as a standalone operating system, they are increasingly being integrated with ERP-systemen (Enterprise Resource Planning). Through this integration, factory managers can ensure timely and cost-effective delivery of high-quality products. The system facilitates data exchange between production and the office.
Here are some ways they collaborate:
- Data integration: MES collects real-time data on production activities and sends it to the ERP system. This provides the ERP system with real-time insights into production performance, allowing for more efficient allocation of company resources.
- Planning: ERP sends production orders to the MES system, which is responsible for planning production processes. The MES system takes into account production capacity, available raw materials, and personnel to create a production plan.
- Inventory management: MES collects real-time data on the quantity of raw materials consumed during production and sends this information to the ERP system. This allows the ERP system to track available raw materials and determine if additional orders are needed.
- Quality control: MES collects and analyzes data on product quality during production and sends this information to the ERP system. This provides the ERP system with insights into product quality, enabling quick identification and resolution of improvement opportunities.
MES and Ignition
Ignition is a modern software platform designed for manufacturing companies to improve production efficiency, quality, and compliance. It is modular, allowing you to pay only for the features you actually need.
Ignition offers a wide library of modules to choose from, including specific MES modules. Some of the key features of these modules include recipe management, planning, production tracking, quality management, and reporting. All aimed at enhancing the efficiency and effectiveness of production activities.
Ignition MES provides a powerful solution for manufacturers looking to optimize their operations, enhance product quality, and increase profitability. By utilizing real-time data and analytics, Ignition helps manufacturers make better-informed decisions and proactively take steps to improve their processes.
What are the advantages of Ignition compared to other MES software?
- Flexibility: Ignition is an open-source platform with a modular design, making it easy to customize to the specific needs of a business.
- Integration: To provide a comprehensive view of all production activities, Ignition offers broad integration capabilities with other systems, including ERP systems, SCADA systems, PLCs and databases. en databases. This enables easy integration and use of data from different systems for production analysis and improvement.
- Cost-effectiveness: Ignition is an open-source platform and is available at lower costs compared to some other MES systems.
- User-friendliness: Ignition features a user-friendly interface and offers a visual and interactive way to analyze and visualize production data.
- Scalability: Ignition is scalable and can be adjusted to meet the growing needs of a business.
Overall, Ignition MES can help manufacturers achieve operational excellence, reduce downtime, minimize waste, and improve product quality.
Hierdoor zijn gegevens uit verschillende systemen eenvoudig te integreren en te gebruiken voor productieanalyses en verbetering.
Discover Ignition
your way
Start building
For developers
Get started with your own Ignition applications right away.
- Download and install Ignition easily and quickly.
- Explore all features.
- Connect unlimited tags, PLCs, databases, and devices.
Discover how Ignition solves your technical challenges without limitations.
See Ignition in action
For managers
Explore Ignition without any technical knowledge in the demo environment.
- No installation required.
- See how Ignition automates and visualizes processes.
- Adjust live values and see instant results.
Experience real-time automation and discover what it can offer your business.
Want to really know what Ignition can do for you?
Let us come to you for a free demo.
- Meet with our experts and ask all your questions.
- Get personalized advice.
- See how Ignition can optimize your processes.
The perfect opportunity to collaborate with specialists and see exactly how Ignition can help you achieve your business goals.