» What is OEE?
» How is OEE calculated?
» What is a good value?
» Who uses it?
» What are the benefits of OEE?
» What are common pitfalls in implementing OEE?
» Why measure OEE with a SCADA-system?
» What is good OEE software?
» OEE and Ignition
» Explore Ignition
Other knowledge base articles
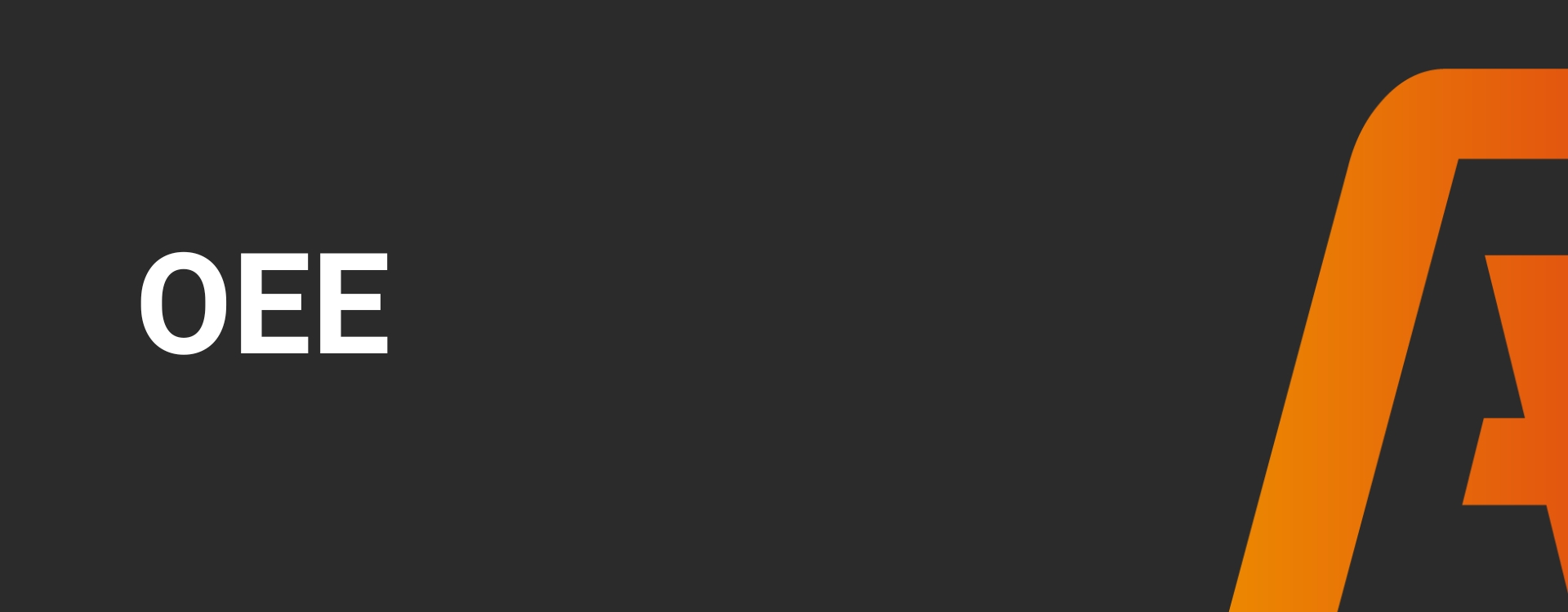
OEE
What is OEE?
OEE stands for Overall Equipment Effectiveness and is the gold standard for measuring production efficiency. It is a measurement method that allows you to gain insight into the actual production time and output. By tracking all downtimes and disruptions, you get an overview of the biggest losses during your production process. All of this is done to prevent these losses and thus increase the OEE score.
The score is calculated based on 3 factors:
- Availability: The percentage of time that equipment is available for production, taking into account both planned and unplanned downtime.
- Performance: The percentage of production capacity being utilized.
- Quality: The percentage of good products produced compared to the total number of products produced.
The OEE value is typically expressed as a percentage, with 100% meaning that the equipment is operating at maximum efficiency. OEE is used to identify areas for improvement, such as equipment that frequently breaks down or processes that yield a high number of defects. By monitoring OEE, manufacturers are able to improve the productivity and profitability of their operations.
How is OEE calculated?
The formula for calculating OEE is as follows:
OEE = availability x performance x quality
1. Availability
If a line is scheduled for an 8-hour shift with two 15-minute breaks and one 30-minute break, then the planned time is 7 hours. If during production there are 25 downtimes totaling 45 minutes of downtime, then the runtime is reduced to 6 hours and 15 minutes. This equates to 7 hours minus 45 minutes. The availability is 89% and is calculated by dividing 6 hours and 15 minutes by 7 hours.
Availability = (total planned production time – unplanned downtime) / total planned production time
2. Performance
If a work cell is designed to produce 10 units per minute, we can calculate the theoretical production. For example, if we take 6 hours and 15 minutes of actual production time and use the example of units produced per minute from above, we produce 3750 units in the given time (6 hours and 15 minutes equals 375 minutes multiplied by 10). If the actual number of units produced is 3000, then the performance is: 3000 divided by 3750, which equals 80%.
Performance = total quantity produced / maximum capacity within the available production time
3. Quality
If out of the total number of units produced from above, 200 units are rejected by quality inspection, you end up with 2800 approved units. The quality then becomes 2800 divided by 3000, which equals 93%.
Quality = total number of good products / total number of products produced
You calculate the OEE score by multiplying all percentages together: 89% x 80% x 93% = 66%.
What is a good value?
A good OEE value depends on the specific equipment or production line being measured and the industry in which it operates. Generally, a value of 85% or higher is considered good, and a value of 90% or higher is considered excellent. However, it’s important to note that achieving a value of 100% is nearly impossible because there are always factors that contribute to downtime or quality issues.
It’s also important to remember that OEE is a relative metric. It should be compared to similar equipment or production lines within your own facility or industry standards, as well as your own historical performance.
Even if you achieve a high value, it doesn’t necessarily mean that the equipment or production line is operating at optimal levels. To truly maximize efficiency and productivity, manufacturers must continuously monitor and analyze OEE data to identify and eliminate bottlenecks and improve performance.
Who uses it?
OEE can be implemented by any company engaged in production activities, regardless of size or sector. It is commonly used in the manufacturing industry, including the automotive, pharmaceutical, food, electronics, and aerospace industries.
Production and operations managers, technical teams, and operators are the primary users. It enables them to measure, analyze, and improve the performance of the production line, leading to increased productivity and profitability.
OEE is also used by other stakeholders within an organization, such as financial managers and business analysts, to measure and assess the overall efficiency of production activities.
What are the benefits of OEE?
- Improved productivity: By identifying and addressing inefficiencies in the production process, productivity is enhanced. This leads to higher output and lower production costs.
- Higher quality: By identifying issues in the production process that affect product quality, product quality improves. This results in less waste and higher customer satisfaction.
- Better planning: It assists in production planning by enabling companies to understand and optimize the capacity of their production lines. This leads to better production scheduling, fewer disruptions, and increased efficiency.
- Lower costs: It reduces production costs by reducing inefficiencies and improving productivity. This results in lower labor costs, energy costs, and material costs.
- Enhanced communication: It improves communication between different departments within a company. By measuring performance and sharing it with other departments, companies can make better decisions and operate more efficiently.
- Continuous improvement: It fosters a culture of continuous improvement within a company. By regularly measuring and improving the performance of the production line, companies enhance their efficiency, quality, and profitability.
What are common pitfalls in implementing OEE?
Implementing OEE can be challenging, and there are several pitfalls that companies need to consider:
- The accuracy of OEE depends on the accuracy of data collection. If incorrect data is collected, this leads to inaccurate calculations. It is important to use the right measurement tools and ensure that staff are properly trained to collect data accurately.
- This is just one performance indicator and should not be the sole focus of a production environment. Placing too much emphasis on improving OEE can detract from other important factors such as quality, safety, and customer satisfaction.
- It is important to set clear goals for OEE improvement and to know what steps need to be taken to achieve these goals. Without clear goals, the implementation of OEE can be chaotic and directionless.
- Successful implementation of OEE requires involvement from the entire team, from operators to management. If employees are not engaged in the process and do not understand why OEE is important, this leads to resistance and a lack of cooperation.
- It is not a static measure, and conditions change regularly. Therefore, it is important to continuously monitor OEE and adjust to changing circumstances, ensuring that improvement measures remain effective.
- It is important to roll this out step by step and not rush. It is tempting to want to see results quickly, but this leads to mistakes and the risk of project failure.
Why measure OEE with a SCADA system?
A SCADA system provides real-time insight into production processes and equipment performance. Through integration with SCADA, operators can monitor equipment performance in real-time and identify trends and issues promptly.
SCADA systems collect data on production and performance of automated equipment. This reduces the need for manual measurements and decreases human errors.
OEE measurements in a SCADA system provide data to improve equipment efficiency and troubleshoot issues. This enables operators and managers to make faster and more informed decisions about optimizing production processes.
Integrating OEE measurements into a SCADA system allows tracking equipment performance over time. This helps identify trends and track performance improvements over time.
What is good OEE software?
There are many software solutions available on the market. The best software depends on the specific needs and requirements of your organization. Here are some key factors to consider when selecting a suitable software solution:
- Ensure that the software provides the functionality you need, such as real-time monitoring, reporting, data analysis, etc.
- Check if the software can be integrated with your existing production and operational systems, such as ERP systems, MES systems, PLCs, etc.
- The software should be easy to use and understand for both technical and non-technical users.
- Ensure that the software is scalable and can be adapted to the growth of your business.
- Check if the software vendor provides sufficient support and training to help your team effectively use the software.
OEE and Ignition
Ignition is a SCADA software platform used for industrial automation and process control. The platform provides functionality for data collection, analysis, visualization, and reporting for various industries, including manufacturing.
Ignition includes an OEE module that allows users to measure and analyze the OEE of their production lines. The module enables real-time monitoring of OEE and provides insight into factors affecting production line performance.
Ignition’s OEE module also features capabilities for capturing and analyzing downtime, measuring product quality, and tracking production rates. This enables users to understand factors influencing OEE and make targeted improvements to increase productivity and profitability.
Why use Ignition for OEE measurements?
- Integration: Ignition offers integration with various automation and production systems, including ERP and MES systems, making it easier to collect and analyze production data.
- Flexibility: Ignition is highly flexible and customizable, making it easy to tailor OEE measurements and reporting to your company’s specific needs.
- Real-time monitoring: Ignition provides real-time monitoring of production lines, enabling operators to quickly identify and resolve issues before they lead to downtime and loss of productivity.
- Analysis: Ignition offers powerful analysis features, allowing users to gain insight into factors affecting OEE and make targeted improvements to increase efficiency.
- Scalability: Ignition is highly scalable, meaning it can be used for small and large production environments and can be adapted to the needs of growing businesses.
- Cost: Ignition is often an affordable solution for OEE measurements compared to other commercial software solutions.
Discover Ignition
your way
Start building
For developers
Get started with your own Ignition applications right away.
- Download and install Ignition easily and quickly.
- Explore all features.
- Connect unlimited tags, PLCs, databases, and devices.
Discover how Ignition solves your technical challenges without limitations.
See Ignition in action
For managers
Explore Ignition without any technical knowledge in the demo environment.
- No installation required.
- See how Ignition automates and visualizes processes.
- Adjust live values and see instant results.
Experience real-time automation and discover what it can offer your business.
Want to really know what Ignition can do for you?
Let us come to you for a free demo.
- Meet with our experts and ask all your questions.
- Get personalized advice.
- See how Ignition can optimize your processes.
The perfect opportunity to collaborate with specialists and see exactly how Ignition can help you achieve your business goals.