» What is an OEM?
» How does an OEM work?
» What are the benefits of an OEM?
» OEM vs. ODM: What is the difference?
» What are the challenges encountered when working with OEMs?
» Trends in usage in industrial automation
» OEM and Ignition
» Explore Ignition
Other knowledge base articles
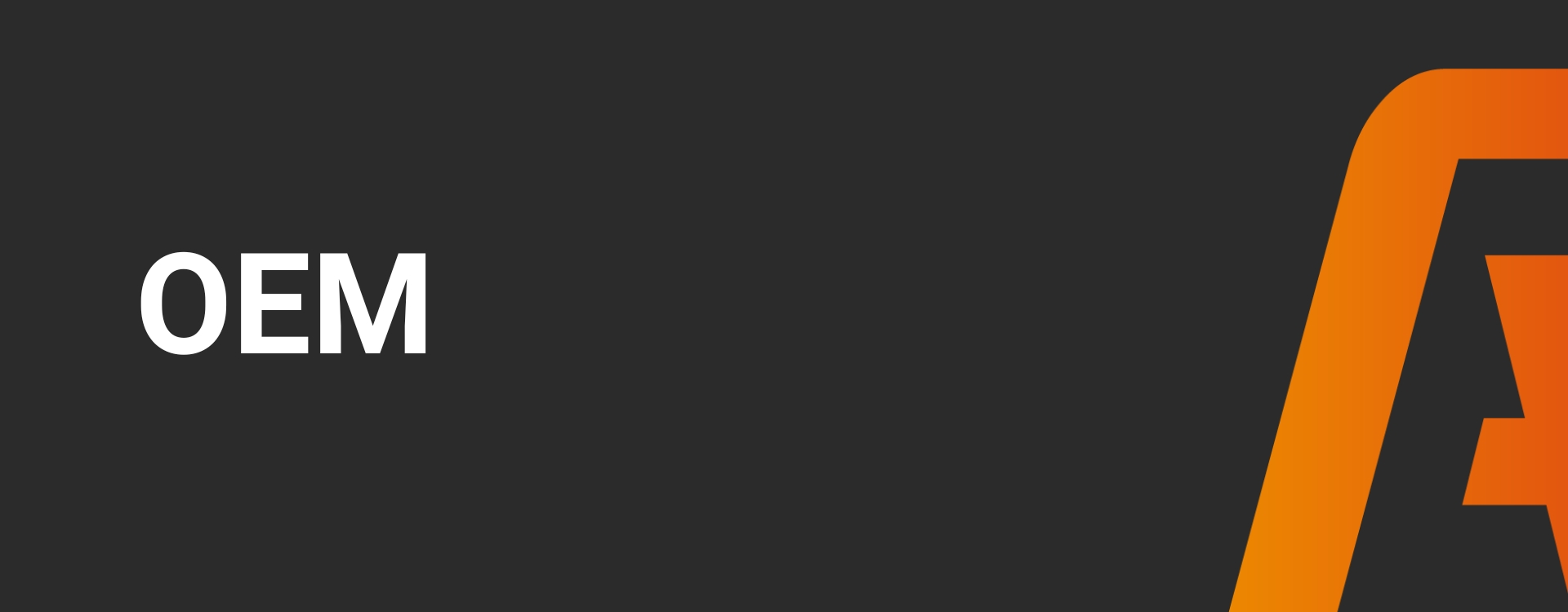
OEM
What is an OEM?
OEM stands for Original Equipment Manufacturer. It is a company that designs and produces components, subsystems, or complete products that other manufacturers then use as part of their own products. An OEM company manufactures parts or subsystems used in the production of another end product and sells them to the manufacturer assembling the final product. Examples of end products include machinery, vehicles, or other goods. OEMs are found in various industries, including the automotive industry, electronics industry, and medical equipment industry.
How does an OEM work?
The OEM process begins when a manufacturer decides to produce a product and determines which parts are needed to make it. The manufacturer then searches for OEMs that produce the required parts.
The OEM then starts designing and manufacturing the requested parts according to the manufacturer’s specifications. The OEM must ensure that the parts are of high quality and meet the manufacturer’s specifications. The company may also offer additional services such as maintenance or repair.
Once the parts or subsystems are produced, the OEM delivers them to the manufacturer, who integrates them into the final product. It is important to thoroughly test and inspect the final product to ensure that it meets the manufacturer’s specifications and quality standards. If everything is in order, the final product is packaged and shipped to end customers.
The OEM process requires good communication and collaboration between the manufacturer and the OEM to ensure that the parts meet specifications and are delivered on time.
What are the benefits of an OEM?
Manufacturers utilize OEMs because they may not always have the expertise or resources to internally design and produce all the parts or subsystems needed for their products. The production of a specific component may be too complex, time-consuming, or the required technology may not be available.
- Cost savings: OEMs are often able to produce parts at a lower cost than the manufacturer themselves. This results in cost savings for the manufacturer, especially if the OEM utilizes more efficient production methods.
- Focus on core competencies: Working with OEMs allows the manufacturer to focus on its core competencies while the OEM handles the production of parts. This allows the manufacturer the space to focus on developing innovative products and improving customer service.
- Flexibility: OEMs are often more flexible than the manufacturer themselves when it comes to producing specific parts. This helps the manufacturer to quickly respond to changes in market demand and to introduce new products to the market.
- Scalability: OEMs are able to scale production capacity up or down depending on the manufacturer’s demand. This helps the manufacturer to adapt to changes in demand and to bring products to market faster.
- Access to expertise: OEMs often have specialized knowledge and experience in production processes and materials. By collaborating with them, the manufacturer gains access to this expertise and has the opportunity to use it to improve products and processes.
OEM vs. ODM: What is the difference?
ODM stands for Original Design Manufacturer. This is a company that not only handles the production of components but also provides design and development services. For example, a company selling consumer electronics would use an ODM to design and develop a new line of products and then bring them to market under its own brand name.
On the other hand, an OEM would only produce the components for this consumer electronics company. The major difference between these two terms is the level of involvement in the design and development process of the product.
What are the challenges encountered when working with OEMs?
Working with OEMs may pose some challenges, including:
- Quality control: The manufacturer must ensure that the OEM produces parts that meet the specifications and quality standards of the manufacturer. It can be difficult to control quality if the OEM is located in a different location.
- Communication: Clear communication with the OEM may be a challenge, especially if there are language or cultural barriers. It is important to ensure that both parties have the same expectations and understand the requirements.
- Price: The price of OEM components sometimes exceeds what the manufacturer expects, especially if there are additional costs such as transportation or customs duties.
- Delivery: Delivery of parts is delayed when there are issues with production or logistics. This disrupts the manufacturer’s production schedule.
- Confidentiality: When the manufacturer shares important intellectual property with the OEM, there is a risk of leakage or misuse of this information. Therefore, it is important to establish confidentiality agreements and adhere to them meticulously.
- Dependency: When the manufacturer relies on one OEM for crucial parts, this leads to a vulnerable position and increases the risk of delays and interruptions in production.
It is important for manufacturers to keep these challenges in mind and work on building a strong and transparent relationship with their OEMs to minimize risks and improve collaboration.
Trends in usage in industrial automation
There are several trends in the use of OEMs in industrial automation. ële automatisering. Customers increasingly demand customized solutions tailored to their production processes and needs. OEMs play a crucial role in this by offering the ability to design and produce customized automation solutions.
Industry 4.0 brings the integration of advanced technologies such as the Internet of Things (IoT), big data, and cloud computing into the production line. OEMs provide solutions that integrate these technologies, enabling the realization of Industry 4.0 benefits such as increased efficiency and productivity.
There is a growing demand for robotics and automation in industrial environments to increase production efficiency and save costs. OEMs offer various types of robots and automation solutions specifically designed for industrial applications.
OEMs are increasingly collaborating with startups to integrate innovative ideas into their industrial automation solutions. These collaborations provide OEMs with the opportunity to develop new and innovative solutions that help improve productivity and efficiency.
Cloud-based solutions provide companies with the ability to remotely access their production processes and data. OEMs offer solutions that utilize cloud-based technologies such as Software-as-a-Service (SaaS) and Platform-as-a-Service (PaaS) to optimize production processes and increase efficiency.
OEM and Ignition
Ignition is a software platform for industrial automation. It offers a wide range of features, including real-time monitoring, data analysis, reporting, mobile access, and more. OEMs can use Ignition as a foundation for developing their own customized automation solutions.
Due to the flexibility of the platform, OEMs can customize Ignition to meet the specific needs of their customers and add new features to their solutions. Ignition also supports the development of custom modules and plug-ins, allowing OEMs to add additional functionality to their solutions and sell them as part of their own product line.
Additionally, Ignition provides tools for managing multiple systems, which is convenient for OEMs delivering solutions to different clients across multiple locations.
In summary, Ignition provides OEMs with the ability to develop their own customized solutions using a robust and flexible software platform, contributing to the improvement of their customers’ productivity, efficiency, and profitability.
Discover Ignition
your way
Start building
For developers
Get started with your own Ignition applications right away.
- Download and install Ignition easily and quickly.
- Explore all features.
- Connect unlimited tags, PLCs, databases, and devices.
Discover how Ignition solves your technical challenges without limitations.
See Ignition in action
For managers
Explore Ignition without any technical knowledge in the demo environment.
- No installation required.
- See how Ignition automates and visualizes processes.
- Adjust live values and see instant results.
Experience real-time automation and discover what it can offer your business.
Want to really know what Ignition can do for you?
Let us come to you for a free demo.
- Meet with our experts and ask all your questions.
- Get personalized advice.
- See how Ignition can optimize your processes.
The perfect opportunity to collaborate with specialists and see exactly how Ignition can help you achieve your business goals.
Start building your own application now!
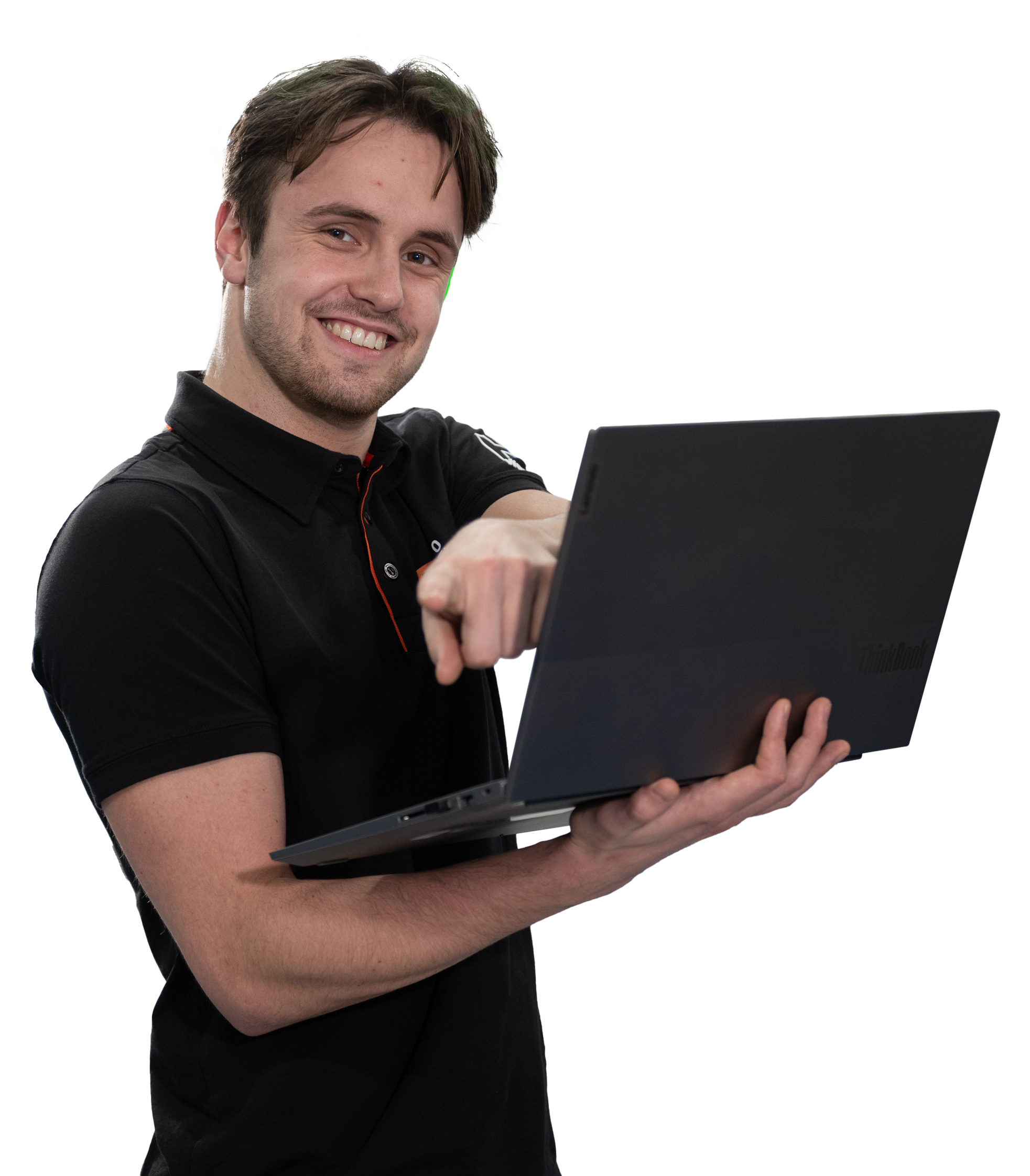
Discover how Ignition can improve your processes!
Want to see how Ignition automates and visualizes processes without any technical knowledge? Fill out the form and gain immediate access to the demo environment, where you can experience Ignition live.
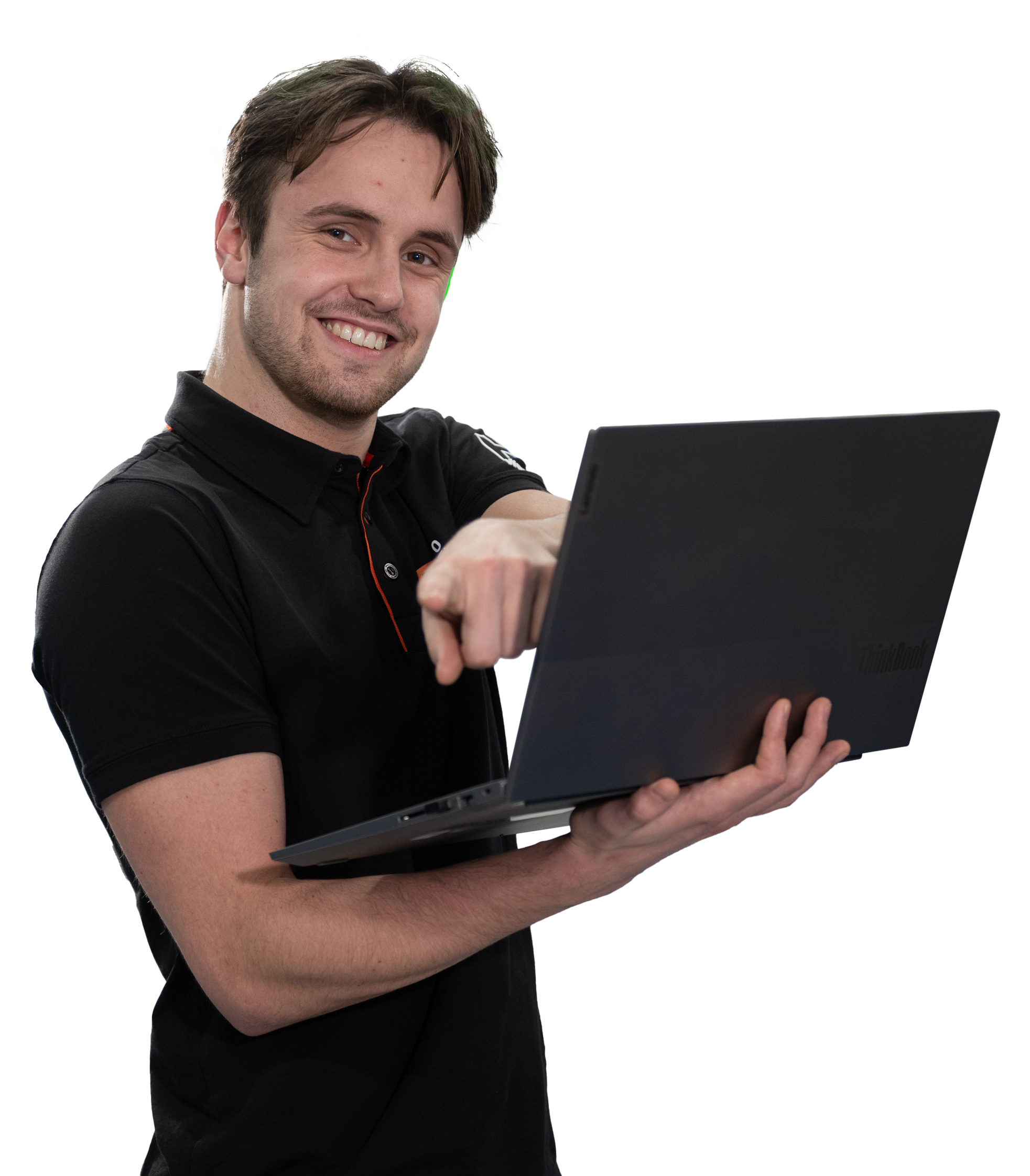
Schedule a no-obligation demo with our experts!
Want to learn more about how Ignition can optimize your processes? Request a personalized demo and discuss your business goals with our specialists. Fill out the form to book an appointment.
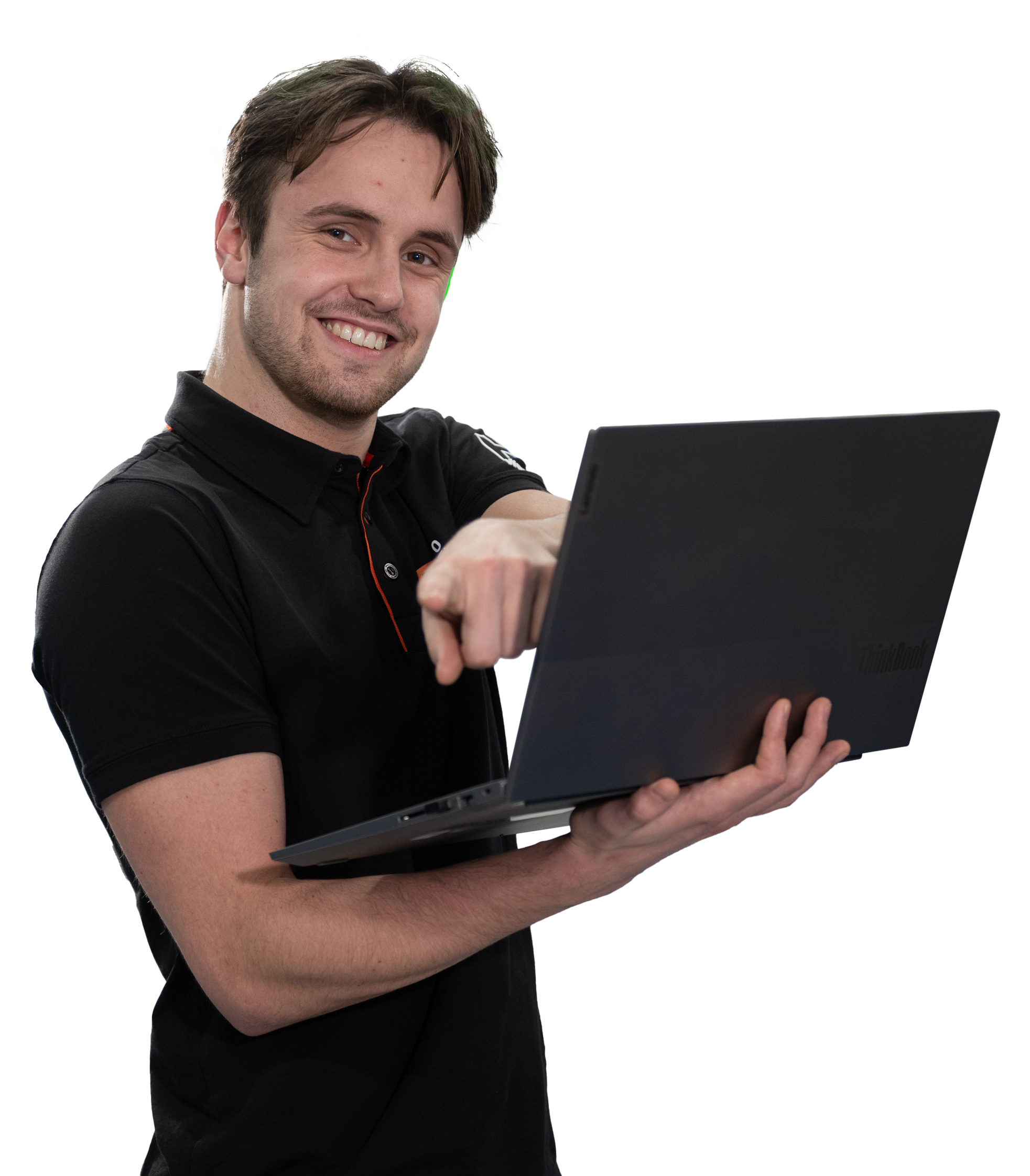