» What is a PLC?
» How does a PLC work?
» Who uses them?
» The benefits of a PLC
» What types are there?
» Safety PLC
» What are the most used brands and why?
» Why should PLC and SCADA collaborate?
» PLC and Ignition
» PLC and IIoT
» The future of PLCs
» When is your PLC outdated?
» Why is it important to replace outdated PLCs in a timely manner?
» Ready to master your growth?
Other knowledge base articles
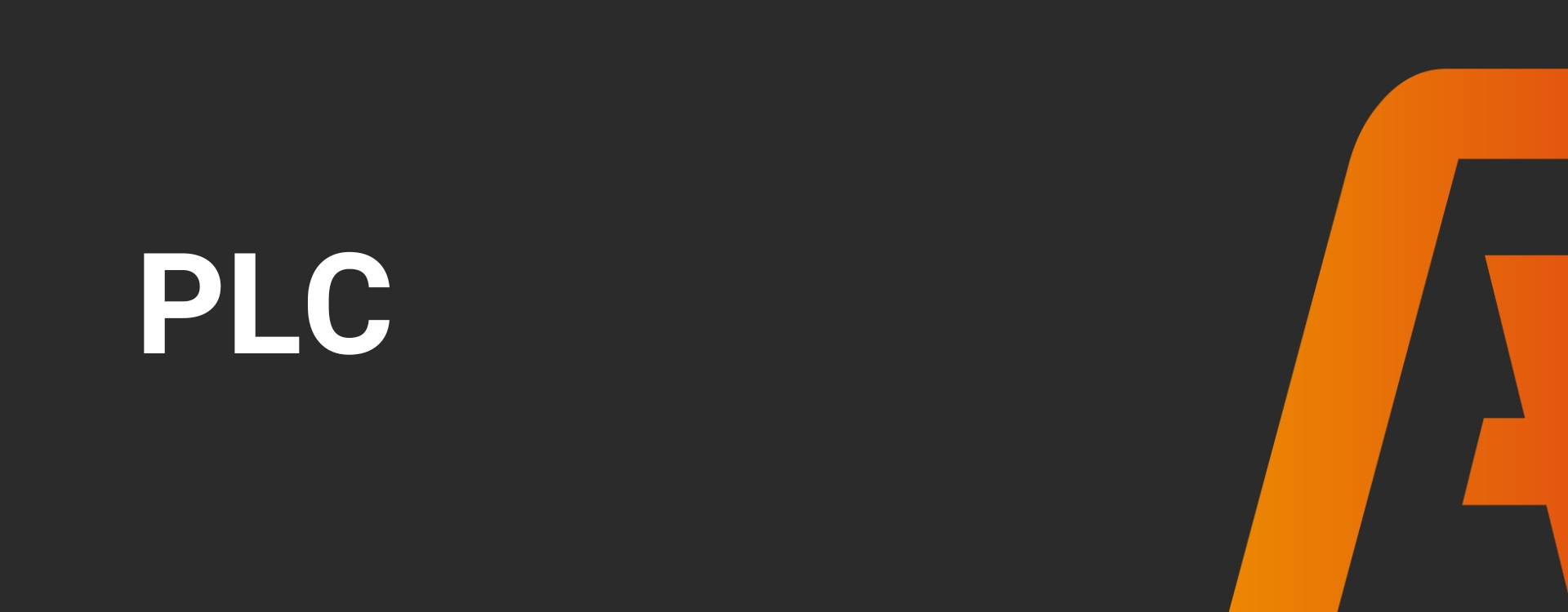
PLC
In this article
» What is a PLC?
» How does a PLC work?
» Who uses them?
» The benefits of a PLC
» What types are there?
» Safety PLC
» What are the most used brands and why?
» Why should PLC and SCADA collaborate?
» PLC and Ignition
» PLC and IIoT
» The future of PLCs
» When is your PLC outdated?
» Why is it important to replace outdated PLCs in a timely manner?
» Ready to master your growth?
What is a PLC?
PLC stands for Programmable Logic Controller. It is a type of industrial computer used to automate various processes in factories, machinery, and other industrial applications.
They are used to receive and process digital and analog signals and to perform logical and mathematical operations on these signals. PLCs are programmable to perform specific tasks and to control machines and processes. Think of regulating the temperature in an oven, controlling a conveyor belt in a production line, or operating a robotic arm.
PLCs are designed to operate reliably in harsh and demanding environments, such as factories where dust, humidity, and vibrations are present. They are also modular and easy to expand and customize to meet the specific requirements of different applications.
How does a PLC work?
A PLC consists of various components that work together to automate an industrial application:
- Input modules: To capture signals from sensors and other devices and convert them into digital signals that the PLC then processes. The signals may contain information about the status of a machine, the position of a sensor, or the temperature in an oven.
- Output modules: To send signals to actuators and other devices to perform a desired action. These may include motors that drive machines, valves that open or close to control fluids, or signal lamps used to provide warnings.
- CPU: The CPU (Central Processing Unit) is the brain of the PLC. It processes the signals coming from the input modules and executes the programs programmed by the programmer.
- Programming: The programmer writes a program that tells the PLC what to do. This program is written in a programming language such as Ladder Logic or Function Block Diagram, and programmed using special software available for the specific PLC.
- Memory: To store the programs written by the user, as well as the values of the variables used in the program.
When a PLC is in operation, the CPU processes the signals coming from the input modules and applies them to the program written by the programmer. The program then determines which actions should be performed by the output modules. This process repeats continuously while the PLC is active, ensuring the control of machines and processes in a reliable and automated manner.
Who uses them?
PLCs are used in various industrial and manufacturing environments where automated processes need to be controlled. This includes:
- Factories and production lines: To control automated processes in factories and production lines, such as assembly, packaging, and manufacturing machines.
- Power plants and utilities: To manage various processes such as water purification, cooling systems, and energy production.
- Traffic control: Traffic lights and other traffic signals are often controlled by PLCs.
- Building automation: To control various systems in buildings, such as HVAC (heating, ventilation, and air conditioning), lighting, and security.
- Transportation and logistics: Including conveyor belts, sorting systems, and automated warehouses.
- Agriculture: To control irrigation systems, animal feeding systems, and other automated processes.
The benefits of a PLC
- Reliability: They are designed to operate in industrial environments and are therefore robust and reliable. They are also resistant to dust, vibrations, humidity, and other environmental factors that may affect the operation of electronic devices.
- Flexibility: They are programmable and adaptable to the specific requirements of a particular application. This allows them to perform various tasks and respond to changing conditions without physical modifications to the equipment.
- Simplicity: They are easy to install, operate, and program using a computer or programming language and have a user-friendly interface.
- Safety: They are designed to operate safely and are used to control complex systems such as traffic lights, elevators, and industrial machinery. Safety is therefore of great importance, and they have built-in safety measures.
- Cost-effectiveness: They are generally cheaper than traditional electronic control systems and are also easy to adapt to the specific requirements of a particular application, resulting in cost savings.
What types are there?
There are different types available on the market, each with specific functions and features designed for various applications. Below is an overview of some common types:
- Compact PLCs: These are suitable for small applications with limited I/O points (input/output). They are typically small in size and contain fewer hardware components than other PLCs.
- Modular PLCs: These have a modular design and offer more flexibility for expansion and upgrades. To meet the needs of a specific application, they can be configured with additional I/O modules and communication cards.
- Programmable relays: This is the first generation still used in some applications. They use electromechanical relays to make circuits and are programmed using Ladder Logic.
- Safety PLCs: These are specially designed for safety applications where the PLC must comply with certain safety standards. They are equipped with safety circuits and special inputs for emergency stops and safety sensors.
- High-end PLCs: These are intended for large, complex applications and offer advanced features such as advanced motion control, built-in diagnostics, and extensive communication capabilities.
- SoftPLCs: These run on a computer platform rather than a hardware controller. They are often used in applications where flexibility and adaptability are important.
The choice of the right PLC depends on the specific application and the required functions and features.
Safety PLC
A safety PLC, also known as Safety PLC, is a type of PLC specifically designed to meet safety requirements and standards. These are used to implement safety-related functions and ensure the safety of workers, equipment, and processes in industrial environments. It is intended to detect and prevent errors in machinery and processes that may lead to accidents and injuries.
They operate in a similar manner to a regular PLC but are equipped with additional hardware and software features to ensure safety. These features include, for example, dual hardware architecture (redundancy) to detect system errors, safety-related instructions designed to comply with safety standards, and built-in safety features such as emergency stops and safety doors.
A safety PLC is often used in applications where there are high risks of injury or equipment damage, such as in the petrochemical industry, automotive industry, aviation industry, and medical industry.
What are the most used brands and why?
There are several brands commonly used in the industry, often depending on the specific application and user preference. Some of the most used brands include:
- Siemens: This is one of the largest manufacturers and offers a wide range of products for various applications. Siemens is often chosen for its reliability, performance, and scalability.
- Allen-Bradley: This is a brand of Rockwell Automation and provides solutions for many different industries. Allen-Bradley is known for its robustness and durability.
- Mitsubishi Electric: They offer PLCs with advanced features and capabilities, such as network integration and powerful programming tools. Mitsubishi Electric is popular for its reliability and performance.
- Omron: This is a leading manufacturer offering a wide range of products for various applications. Omron is known for its high quality and reliability.
- ABB: This is a leading manufacturer providing solutions for industrial automation. ABB is known for its reliability, scalability, and performance.
Why should PLC and SCADA collaborate?
SCADA (Supervisory Control and Data Acquisition) is also a crucial component of an industrial automation system. Although it serves different functions, it is essential for it to work together with PLCs to create an effective and efficient system.
PLCs are responsible for collecting and processing data from sensors and actuators in the field, while SCADA systems collect, analyze, and visualize this data in the control room. By gathering and analyzing data from PLCs, SCADA can provide vital information about the performance of machines and processes and detect issues before they occur.
A PLC provides the necessary control and automation for industrial processes. On the other hand, SCADA systems offer a high level of supervision and remote control, allowing operators to manage the entire system from a central location. Integrating both systems enables operators to monitor key process parameters and make adjustments from the control room.
The use of both systems makes processes more efficient and productive. By analyzing the collected data, SCADA improves process efficiency and increases productivity.
Both systems are also crucial for the safety of workers and machines in the factory. By analyzing the collected data, SCADA enhances the safety of the work environment and enables quick responses to potential issues or emergencies.
It can be said that the collaboration between these components is crucial for the effectiveness and efficiency of industrial automation systems. By integrating these two systems, manufacturers can improve the performance of machines and processes, ensure the safety of the work environment, and increase company productivity.
PLC and Ignition
Ignition is a software platform used to design, develop, and deploy SCADA and HMI applications. PLCs can be integrated into Ignition systems to collect and control data. Ignition communicates with PLCs via various protocols such as Modbus, OPC-UA of Siemens S7. This allows Ignition to collect data from PLCs and visualize it in HMI screens and dashboards.
Ignition enables monitoring and control of automated processes from a central location. With Ignition, operators can view data, analyze trends, set alarms, and generate reports. It also provides the ability to analyze data and use it for predictive maintenance and process optimization.
Ignition is a highly flexible and configurable platform for designing and developing custom HMI and SCADA applications. It also offers integration capabilities with other systems such as ERP and MES systems, allowing integration and use of data from various sources.
In short, PLCs and Ignition work together to control and monitor automated processes. Ignition provides a powerful HMI/SCADA solution for visualizing and managing data from PLCs. By combining these two technologies, you can improve the performance and efficiency of your industrial automation systems.
PLC and IIoT
PLCs and IIoT (Industrial Internet of Things) are two technologies that are increasingly being combined to create smart, integrated, and efficient production processes. Below are some ways in which PLCs and IIoT work together:
- Data collection: PLCs can be used to collect data from various sensors and actuators integrated into a production line. This data can be analyzed to gain insight into equipment performance and to detect problems before they lead to downtime.
- Communication: PLCs can communicate with other devices in the production line, such as HMIs, SCADA systems, and other PLCs. This allows for more efficient management of the production line and quicker problem resolution.
- Cloud connectivity: PLCs can be connected to cloud-based platforms, such as Microsoft Azure or AWS, to send and receive data. This provides real-time insight into production line performance, improving efficiency and reducing downtime.
- Analysis and prediction: By using machine learning algorithms, data collected by PLCs can be analyzed to gain insight into equipment performance and predict potential failures. This can help make the production line more efficient and minimize downtime.
- Cybersecurity: PLCs can be secured using IIoT technologies such as blockchain and secure communication protocols to ensure the integrity and security of the production line.
By harnessing the power of IIoT and PLCs, manufacturers can make their production lines more efficient, safer, and more reliable. This can result in higher productivity, lower costs, and better customer satisfaction.
The future of PLCs
This technology has been crucial in industrial automation for decades and will continue to play a significant role in the future. Some trends influencing this are:
Industry 4.0
The trend towards Industry 4.0 and the integration of intelligent machines and production systems are increasing the demand. PLCs play a crucial role in collecting and processing data from sensors and communicating with other machines and systems.
Edge computing
Edge computing, where data is processed at the location where it is generated rather than on an external server, enhances the performance of PLCs. This is especially important for applications where real-time data processing is essential.
Safety
Safety remains a significant focus when designing and implementing PLC systems. Future PLCs will provide even more advanced safety features to ensure the safety of workers, machines, and processes.
Cloud computing
Cloud computing offers the ability to collect and analyze PLC data on a scale previously not possible. This leads to new applications and usage possibilities for PLCs.
Artificial intelligence
The integration of AI (Artificial Intelligence) into PLC systems improves the efficiency and performance of these systems. This results in better automation of processes and improved quality of the products produced.
When is your PLC outdated?
A PLC becomes outdated for various reasons, including:
- Technological advancements: Technologies used in PLCs are constantly evolving, resulting in new and improved features. If your PLC does not support these new features, it means that your PLC is outdated.
- Manufacturer support: When the manufacturer of your PLC no longer provides technical support or supplies replacement parts, it is a sign that your PLC is outdated.
- End-of-life announcement: When the manufacturer announces that a particular model or series of PLCs is no longer being produced, it means that the PLC is outdated and will soon be unavailable.
- Availability of spare parts: When spare parts for your PLC are no longer available or difficult to find, it means that your PLC is outdated and will soon no longer be supported.
- Changes in production: When your production process changes and your PLC no longer meets the requirements, it means that your PLC is outdated.
If one or more of the above factors apply to your PLC, it may be time to consider upgrading to a newer model. This helps to improve the efficiency and reliability of your production line and also ensures the availability of technical support and spare parts in the long term.
Why is it important to replace outdated PLCs in a timely manner?
It is important to replace outdated PLCs in a timely manner for several reasons:
- Safety: Outdated PLCs are vulnerable to security risks, allowing hackers to take control and sabotage equipment. Newer PLCs often have better security features to ensure safety.
- Reliability: Outdated PLCs become less reliable as they age, increasing the risk of malfunctions and downtime. This leads to unplanned production line shutdowns and loss of production.
- Maintenance costs: If spare parts and technical support for outdated PLCs are harder to find, repairing the equipment becomes more expensive and time-consuming.
- Efficiency: Newer PLCs often have better features and capabilities to improve production line efficiency, such as faster processing times and better data collection and analysis.
- Compliance: Outdated PLCs may not meet the latest regulations and standards for production, potentially causing companies to fail to comply with industry or government requirements.
By replacing outdated PLCs in a timely manner, a production line remains safer, more reliable, more efficient, and compliant with the latest standards and regulations. This helps to reduce costs and improve profitability by reducing production loss and repair costs, and improving productivity and quality.
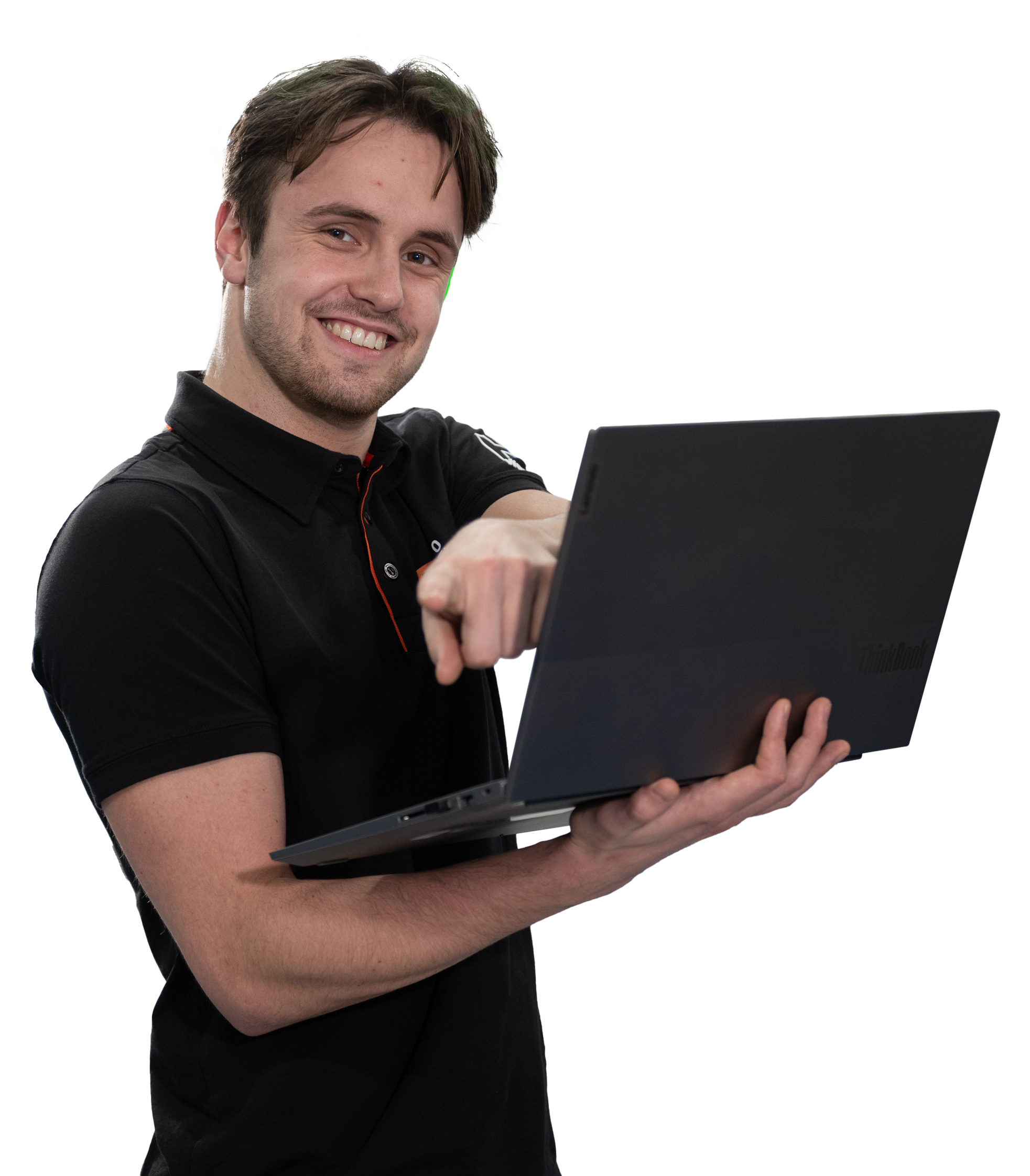
Ready to master your growth?
At AT-Automation, we aim to accelerate your growth and reach new heights of efficiency with our advanced automation solutions. We strongly believe in sharing knowledge and empowering individuals to become masters in industrial automation. Would you like free advice on how our solutions can help your business grow? Please leave your contact information below.
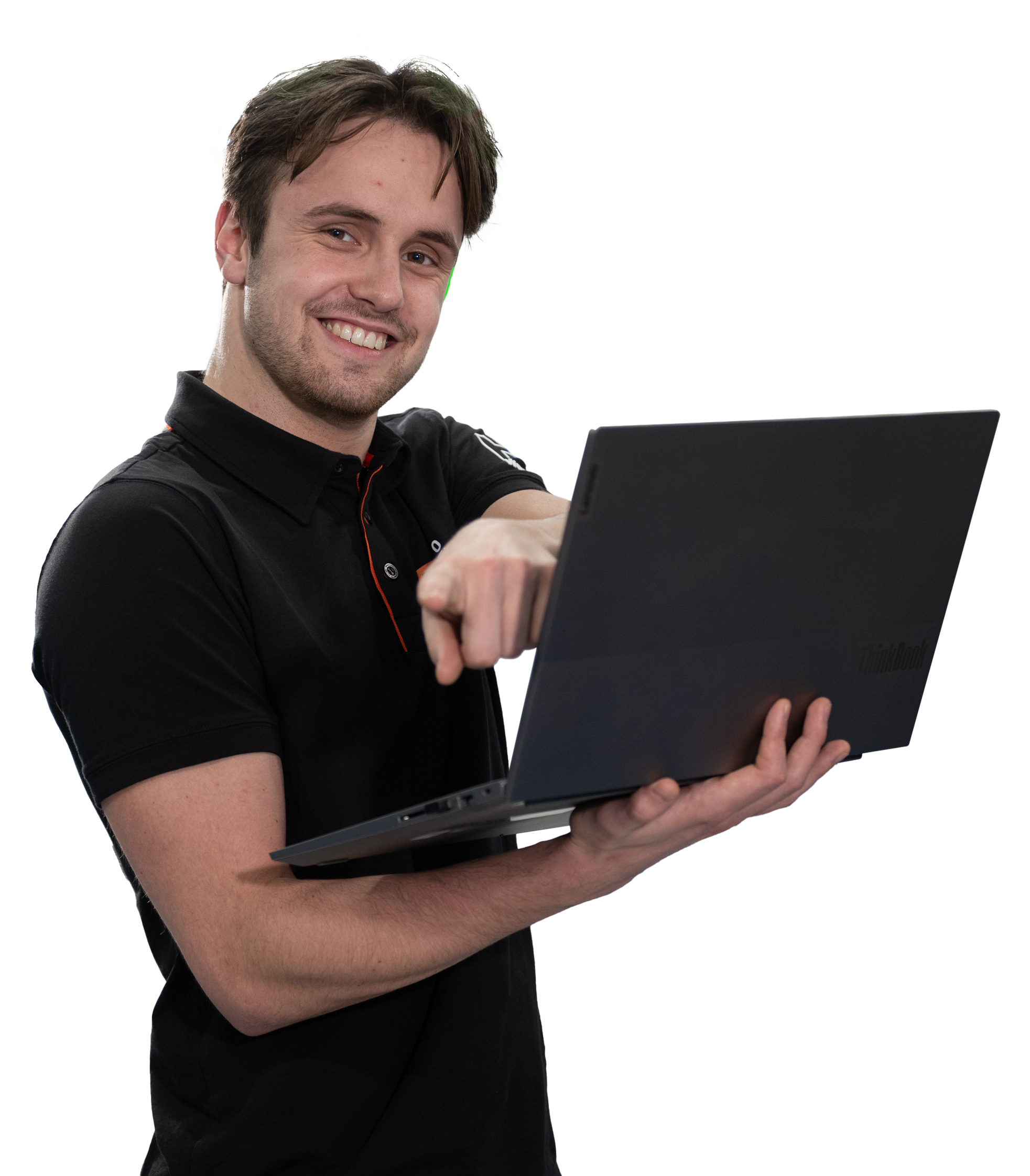