» What is a retrofit?
» Which machines and equipment are suitable for retrofitting?
» What are the advantages of retrofitting compared to purchasing new machines?
» What are the costs of a retrofit and how do they compare to the costs of purchasing new machines?
» How does the retrofitting process unfold from start to finish?
» What factors should you consider when planning a retrofit?
» How do you measure and evaluate the performance of a retrofitted machine?
» Examples of some succesful retrofits in the industry
» Ready to master your growth?
Other knowledge base articles
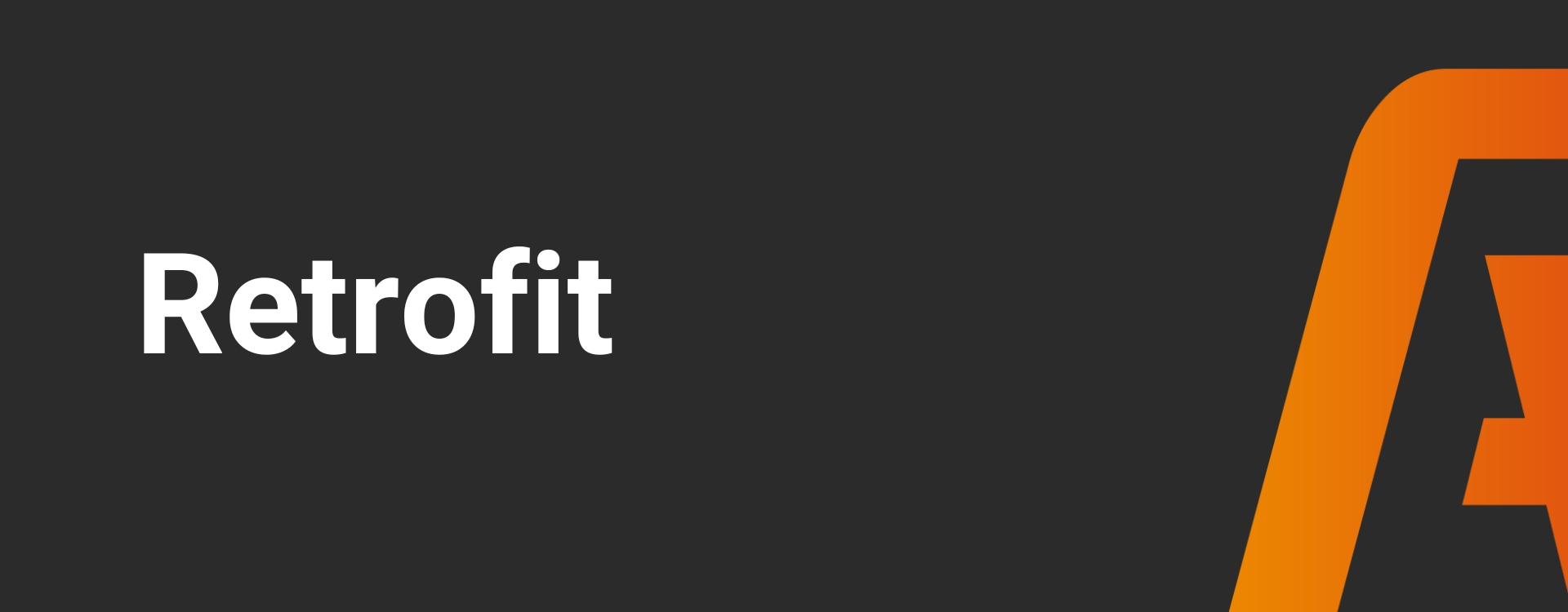
Retrofit
In this article
» What is a retrofit?
» Which machines and equipment are suitable for retrofitting?
» What are the advantages of retrofitting compared to purchasing new machines?
» What are the costs of a retrofit and how do they compare to the costs of purchasing new machines?
» How does the retrofitting process unfold from start to finish?
» What factors should you consider when planning a retrofit?
» How do you measure and evaluate the performance of a retrofitted machine?
» Examples of some succesful retrofits in the industry
» Ready to master your growth?
What is a retrofit?
In the industry, a retrofit refers to the process of adapting or modernizing existing machinery, equipment, or systems with new technologies, components, or features. The ultimate goal is to improve performance, extend lifespan, and make it compatible with new industry standards. Companies opt for a retrofit because it is often a cost-effective alternative to purchasing new machines or equipment, especially when the existing machine is still in good condition and only certain components or systems require replacement or upgrade. The aim of retrofitting is to enhance efficiency and productivity, reduce operational costs, and increase the sustainability of machinery and equipment.
Which machines and equipment are suitable for retrofitting?
In principle, almost any machine or device is suitable for a retrofit as long as it is still in good condition and suitable for the intended application. Some examples of suitable machines and devices include:
- Production lines: Retrofitting production lines leads to better quality, efficiency, and flexibility in production processes.
- Packaging machines: Retrofitting packaging machines results in better and faster packaging, leading to more efficient processes and less waste.
- Robotics: Retrofitting robots leads to improved performance, higher precision, and better control over robot movement.
- HVAC systems: Retrofitting HVAC systems leads to energy savings and more efficient heating, ventilation, and air conditioning.
- Lighting: Retrofitting lighting systems leads to energy savings and better lighting, improving the safety and productivity of workers.
What are the advantages of retrofitting compared to purchasing new machines?
- Cost-saving: Retrofitting is often cheaper than purchasing new machines. It helps to extend the lifespan of existing machines and adapt them to the latest technologies and standards.
- Sustainability: Contributes to sustainability by extending the lifespan of existing machines and reducing the need to produce new ones. This, in turn, helps to reduce waste and conserve natural resources.
- Improved performance: Upgrades existing machines with new technologies, improving performance and increasing productivity.
- Reduced downtime: By adapting machines to the latest technologies and standards, the risk of malfunctions and downtime is reduced.
- Quick implementation: Retrofitting is often faster to execute than purchasing and installing new machines. This allows companies to quickly resume production and minimize production process downtime.
What are the costs of a retrofit and how do they compare to purchasing new machines?
The costs of a retrofit can vary significantly depending on various factors such as the scope of the project, the complexity of the equipment, the required materials, and labor costs. However, generally speaking, retrofitting is significantly cheaper than purchasing new machines.
Acquiring new machines often involves substantial costs, including production and delivery costs, installation, training, and maintenance of the new equipment. Additionally, new machines may incur higher energy costs than older, retrofitted machines, potentially leading to increased operating costs in the long run.
While the initial costs of a retrofit may appear higher than the costs of a simple repair, the benefits of retrofitting such as increased efficiency, reliability, and safety, along with the extended lifespan of the equipment, have a significant impact on the profitability of the business in the long term. Therefore, it is important to conduct a thorough cost-benefit analysis to determine if a retrofit is the best option for a specific situation.
How does the retrofitting process unfold from start to finish?
The retrofitting process varies depending on the type of machine or equipment and the project requirements. Generally, it involves the following steps:
- The process begins with an evaluation of the existing machine or equipment. This is a crucial first step to determine if a retrofit is feasible and what modifications are needed.
- The next step is to specify all necessary changes and upgrades in a retrofitting plan. This includes new control and drive systems, sensors, or other components.
- Upon approval of the plan, the installation of the new components and systems begins. This process is often time-consuming and may take weeks or months, depending on the project’s scope.
- Once the installation is complete, thorough testing is conducted to ensure that it operates correctly and meets the requirements.
- Training may be necessary to ensure that personnel can operate the “new” machine or equipment properly.
- Regular maintenance is then performed to preserve its operation and efficiency.
What factors should you consider when planning a retrofit?
When planning a retrofit project, several factors need to be taken into account. Some important factors include:
- Objectives: These should be clearly defined. For example: energy savings, reduction of greenhouse gas emissions, improvement of air quality, enhancement of residents’ comfort, or increasing the value of the building.
- Budget: This is crucial as it will determine which measures are feasible or not. An accurate cost estimate and cost-benefit analysis are essential.
- Technical feasibility: It’s important to investigate and determine which technologies and materials are most suitable for the specific needs of the building.
- Legal aspects: There may be applicable regulations, such as permits, building safety regulations, and any subsidy programs.
- Planning and timelines: It’s important to establish these realistically, considering all steps such as design, financing, implementation, and evaluation.
- Monitoring and evaluation: It’s crucial to develop a plan for this as well. This allows you to monitor whether the project has achieved its objectives and to identify and address any issues that may arise.
How do you measure and evaluate the performance of a retrofitted machine?
Step 1: Start by gathering data on the machine’s performance before the retrofit and then after the retrofit. Collect data on productivity, quality, efficiency, energy consumption, and downtime.
Step 2: Next, define the key performance indicators (KPIs) you want to measure and evaluate, such as cycle time, production speed, error rate, energy consumption, and downtime. These KPIs will help quantify and compare the machine’s performance before and after the retrofit.
Step 3: Analyze the data to assess the performance of the retrofitted machine and compare it to the performance before the retrofit. Compare cycle times to see if they have shortened after the retrofit, or compare energy consumption to see if it has decreased.
Step 4: Identify areas where the retrofitted machine still needs improvement and take action to address them. This may involve implementing new processes or procedures, or integrating new technologies or software to further enhance performance.
Step 5: Create a report presenting the results of the retrofit and describing the improvements achieved. This report serves as a basis for further optimization and as a reference point for future retrofit projects.
Examples of some succesful retrofits in the industry
Here are some examples of successful retrofit projects in industrial automation to inspire what the possibilities are:
Packaging line retrofit
A food manufacturer wanted to modernize its packaging line to increase production and improve the quality of the end product. The retrofit project involved installing new sensors, control systems, and software, and integrating advanced automation technologies such as vision systems and robotics. The result was a packaging line that operates more efficiently, produces less waste, and delivers higher quality end products.
Combined heat and power (CHP) system retrofit
An industrial manufacturer wanted to improve its energy efficiency and reduce greenhouse gas emissions by installing a combined heat and power (CHP) system. The retrofit project involved replacing old turbines and engines with new, more efficient models, installing heat recovery systems, and integrating advanced control technologies. The result was a CHP system that increased the factory’s energy efficiency and reduced greenhouse gas emissions.
Robot cell retrofit
A metal products manufacturer wanted to modernize its production process by installing a robot cell to automate production. The retrofit project involved integrating a new robot, new sensors and software, and incorporating advanced control technologies such as vision systems and machine learning algorithms. The result was a robot cell that operates more efficiently, produces less waste, and increases production.
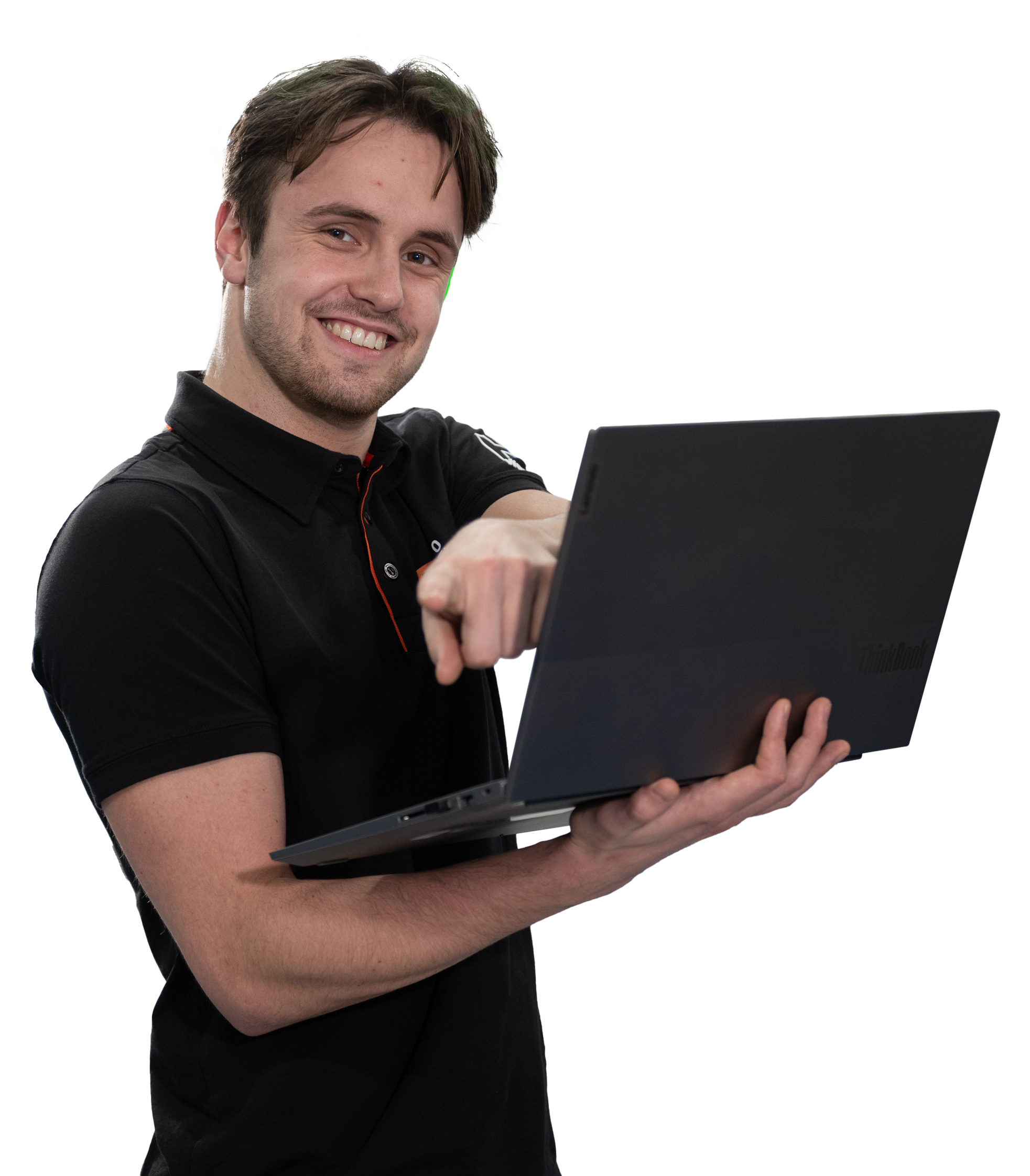
Ready to master your growth?
At AT-Automation, we aim to accelerate your growth and reach new heights of efficiency with our advanced automation solutions. We strongly believe in sharing knowledge and empowering individuals to become masters in industrial automation. Would you like free advice on how our solutions can help your business grow? Please leave your contact information below.
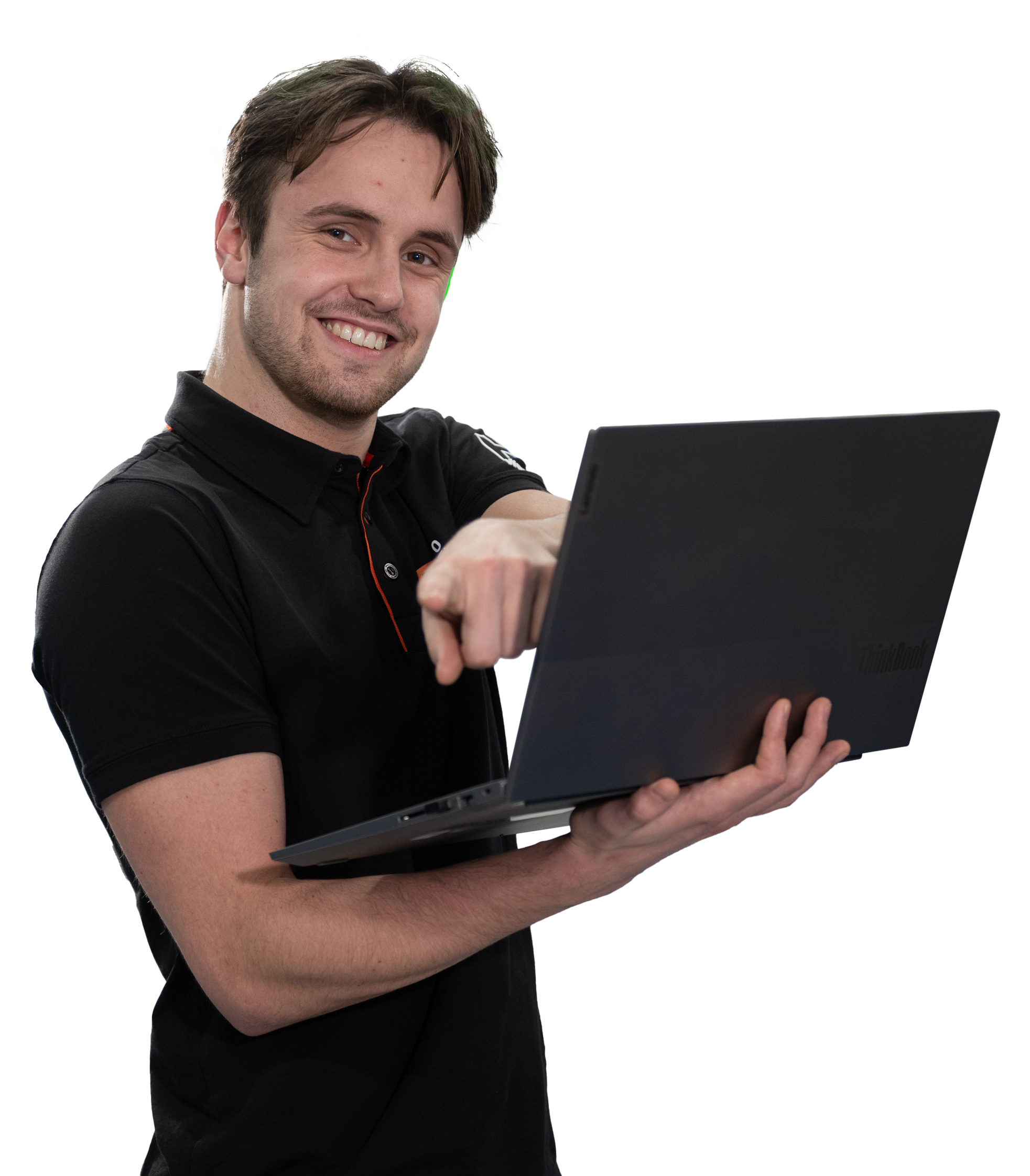