» What is a robot?
» How do robots work?
» What are the applications of industrial robots?
» What are the benefits of using them in the industry?
» Are there any drawbacks to using robots in the industry?
» How do industrial robots contribute to sustainability and environmental protection?
» What is the difference with a cobot?
» What does the future of industrial robots look like?
» Ready to master your growth?
Other knowledge base articles
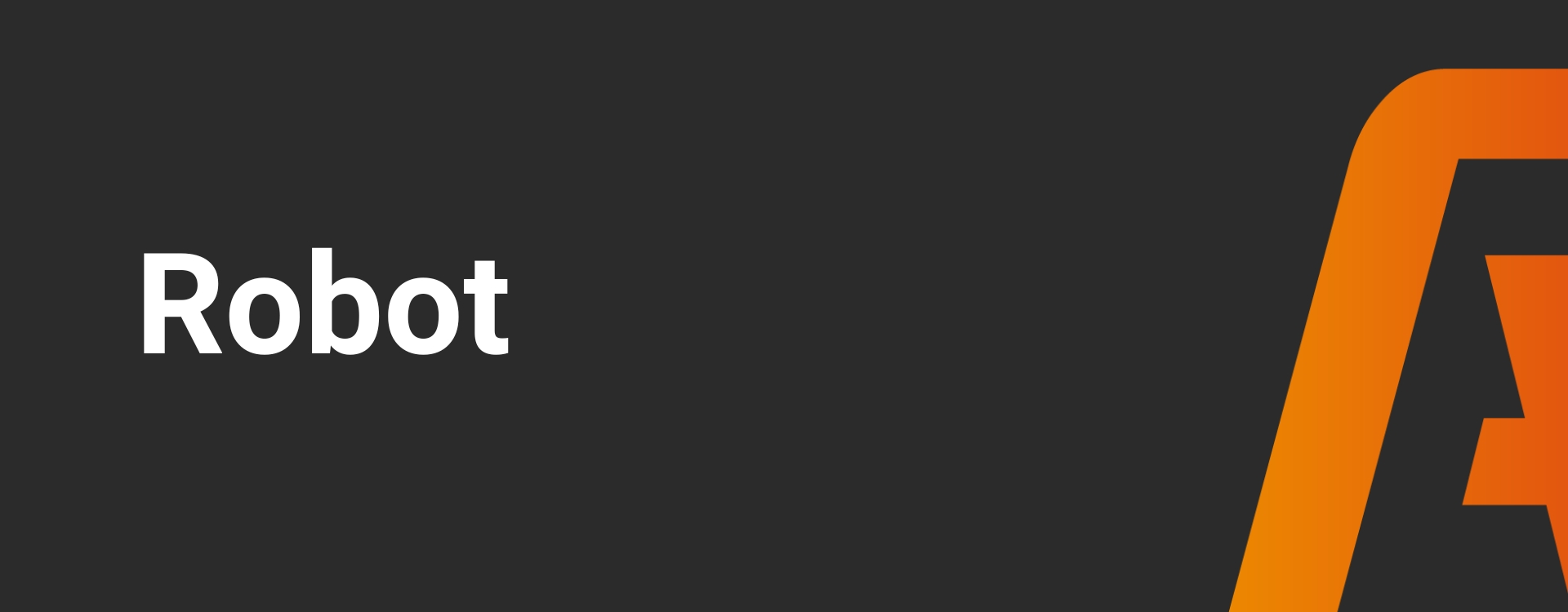
Robot
In this article
» What is a robot?
» How do robots work?
» What are the applications of industrial robots?
» What are the benefits of using them in the industry?
» Are there any drawbacks to using robots in the industry?
» How do industrial robots contribute to sustainability and environmental protection?
» What is the difference with a cobot?
» What does the future of industrial robots look like?
» Ready to master your growth?
What is a robot?
A robot is a programmable machine capable of performing tasks and interacting physically with its environment. Generally, a robot possesses the following characteristics:
- A robot consists of mechanical components such as sensors, actuators, and motion mechanisms, enabling it to move and act in the physical world.
- Robots can be programmed with instructions, algorithms, or software code, allowing them to perform specific tasks. This flexibility enables robots to perform various tasks without physical modifications.
- While the level of autonomy varies, robots often have the ability to make decisions and take actions without continuous human intervention. They respond to the environment and adapt to changing conditions.
- Robots can interact with the physical world through sensors and actuators. They gather information from their surroundings, such as images, sounds, or touches, and respond to them through movement, sound, or other forms of output.
They are designed to perform tasks that are dangerous, repetitive, complex, or impossible for humans, and have the potential to improve efficiency, productivity, and quality in various industries.
How do robots work?
Robots are equipped with various sensors that enable them to gather information about their surroundings. These include cameras, microphones, pressure sensors, motion sensors, and touch sensors. These sensors detect physical changes such as images, sounds, pressure, motion, or temperature, and convert them into usable data.
The robot controller, a computer or microcontroller, processes the collected sensor data. It executes algorithms and software code that provide the robot with instructions on how to respond to specific situations.
Robots have actuators, such as motors, servo motors, or hydraulic cylinders, which are responsible for the physical movement and interaction of the robot with the environment. The robot controller sends signals to the actuators to perform the desired movements or actions. This includes moving joints, grasping objects, rotating wheels, or executing complex movements.
Robots are programmable using software. This involves defining motion paths, responses to sensor data, and other behaviors. Some robots also utilize AI algorithms, enabling them to learn and adapt to new situations.
Note: The exact operation of a robot varies greatly depending on the type and specific application.
What are the applications of industrial robots?
Industrial robots have numerous applications in various sectors of manufacturing and production. Some common applications of industrial robots include:
- Assembly: To join components and assemble products. They perform complex and repetitive tasks with high accuracy and speed.
- Welding: For welding operations in the automotive industry, shipbuilding, and other metalworking industries. They weld with consistent quality and precision, resulting in stronger and better-welded structures.
- Packaging: For packaging products in boxes, crates, or other packaging materials. They are capable of sorting, stacking, palletizing, and preparing products for shipment. This increases the efficiency and speed of the packaging process.
- Handling and material transport: For handling and moving materials and objects within production facilities. For example, they can pick up materials from a conveyor belt, load and unload machines, manage warehouses, and perform logistical tasks.
- Quality control: For quality control processes such as inspection, measurement, and defect detection. They perform visual inspections, make accurate measurements, and identify defective products. This helps to ensure the quality and consistency of products.
- Painting and finishing: For spraying and applying paint, coatings, and finishing layers to products and surfaces. They achieve even, precise, and uniform finishes, resulting in better quality and aesthetics.
- CNC machining: For precision machining of materials such as milling, drilling, cutting, and grinding. This improves productivity and reduces the chance of human error.
What are the benefits of using them in the industry?
- Increased productivity: They perform tasks at high speed and accuracy, benefiting the productivity of industrial processes. They work 24/7 without getting tired, thereby increasing production efficiency.
- Improved quality: They perform tasks consistently according to predefined parameters. This improves the quality of products and processes. They reduce human errors and variability, resulting in more reliable and consistent output.
- Safety: They take over hazardous tasks and environments, reducing the risk of workplace accidents and injuries for employees. They follow safety protocols and comply with strict safety standards.
- Cost savings: While the initial investment in robots may be high, they deliver cost savings in the long run. Robots reduce the need for human labor, resulting in lower labor costs. Additionally, they improve efficiency, optimize energy consumption, and reduce waste.
- Flexibility and adaptability: Robots are programmable and adaptable to different tasks and production processes. They can be quickly reprogrammed and redeployed for various tasks. This increases production flexibility.
Are there any drawbacks to using robots in the industry?
- High initial costs: Purchasing, installation, and programming may entail significant initial costs. This is particularly challenging for smaller companies with limited financial resources.
- Technical complexity: Programming and maintenance require technical expertise. Companies may need to invest in specialized knowledge and training to effectively use and maintain the robots.
- Reduced labor demand: While capable of taking over labor-intensive tasks, this may lead to job loss for human workers. This has social and economic implications, especially in sectors where human labor is traditionally prevalent.
- Limited flexibility: While flexible within their programmed tasks, they may have limitations in handling unexpected situations or tasks that require complex human skills, such as creativity and problem-solving ability.
- Maintenance and repairs: They require regular maintenance and repairs to maintain optimal performance. This entails additional costs, especially if spare parts are difficult to obtain or specialized technicians are required.
It is essential to conduct a thorough cost-benefit analysis and risk assessment before a company decides to deploy robots.
How do industrial robots contribute to sustainability and environmental protection?
Industrial robots contribute to sustainability and environmental protection in multiple ways. They are often designed to operate energy efficiently, with precise and controlled movements that minimize energy waste compared to human labor or less advanced machines.
Additionally, they can be programmed to apply energy-saving strategies, such as minimizing unnecessary movements and optimizing the production cycle.
Furthermore, robots contribute to waste reduction and material efficiency. Their precise and consistent operation reduces the number of errors and defects, resulting in fewer rejected products and a minimization of raw material usage. Robots also assist in recycling and reusing materials, reducing overall environmental impact.
Industrial robots increase productivity by performing tasks faster and more efficiently. This leads to a reduction in total production time and energy consumption per unit produced. By optimizing and automating processes, robots maximize production capacity and minimize waste.
The use of industrial robots also enhances worker safety and health. They can be deployed in hazardous environments or for physically demanding tasks, protecting workers from risks and injuries. This contributes to employee well-being and reduces health and safety impacts.
Moreover, robots can be integrated with advanced data analytics techniques and artificial intelligence. This enables companies to collect and analyze data on production processes, efficiency, and energy consumption. With these insights, companies can improve their performance, identify bottlenecks, and implement optimizations for a more sustainable and environmentally friendly operation.
What is the difference with a cobot?
A robot is an autonomous or semi-autonomous machine programmed to perform certain tasks. Robots have various forms of interaction with humans, such as receiving commands, communicating through speech or screens, and performing tasks without direct human intervention.
On the other hand, a cobot, or collaborative robot, is a specific type of robot designed to safely collaborate with humans. They are focused on supporting human workers and improving human-robot collaboration.
Unlike traditional robots, cobots are specifically designed with safety in mind, allowing them to work alongside humans without the need for protective barriers or fences. They often feature softer materials and rounded shapes to prevent injury in case of collision. Cobots utilize advanced sensors and technologies to detect the presence of humans and adjust their movements accordingly, enabling them to safely collaborate.
Cobots are characterized by their flexibility and adaptability. They are easily reprogrammable and reconfigurable to perform various tasks in collaboration with humans. This makes them particularly suitable for tasks that vary in complexity or require regular interaction with human workers.
What does the future of industrial robots look like?
The future of industrial robots looks promising, with new technological developments and trends paving the way for further progress and adoption.
Collaborative robots, or cobots, are specifically designed to work safely alongside humans in a shared work environment. Equipped with sensors and software, they detect human presence and adjust their movements to prevent collisions. This makes them ideal for industries such as manufacturing, logistics, and healthcare, where human-robot collaboration is essential.
In addition to working alongside humans, robots are also becoming increasingly autonomous, capable of performing complex tasks independently. By learning from experiences, adapting to changing conditions, and making decisions based on data analysis and artificial intelligence (AI), robots contribute to greater efficiency, flexibility, and adaptability in industrial environments.
Robots are also becoming more integrated into larger systems of connected devices, such as the Industrial Internet of Things (IIoT). By sharing data, communicating, and collaborating with other machines and systems, robots contribute to more integrated and optimized production processes.
The development of advanced sensor technologies, including vision systems, enables robots to perceive and understand their environment more accurately. This allows robots to perform complex tasks that require precise perception and interaction with the environment.
At the same time, there is a strong emphasis on human-centric design approaches. Robots are designed with user-friendly interfaces, natural language processing, and intuitive programming tools, making them more accessible to non-technical users.
Finally, robots are becoming increasingly modular, making them easier to adapt to different tasks and environments. This increases the deployability of industrial robots and reduces the costs of adjustments and upgrades.
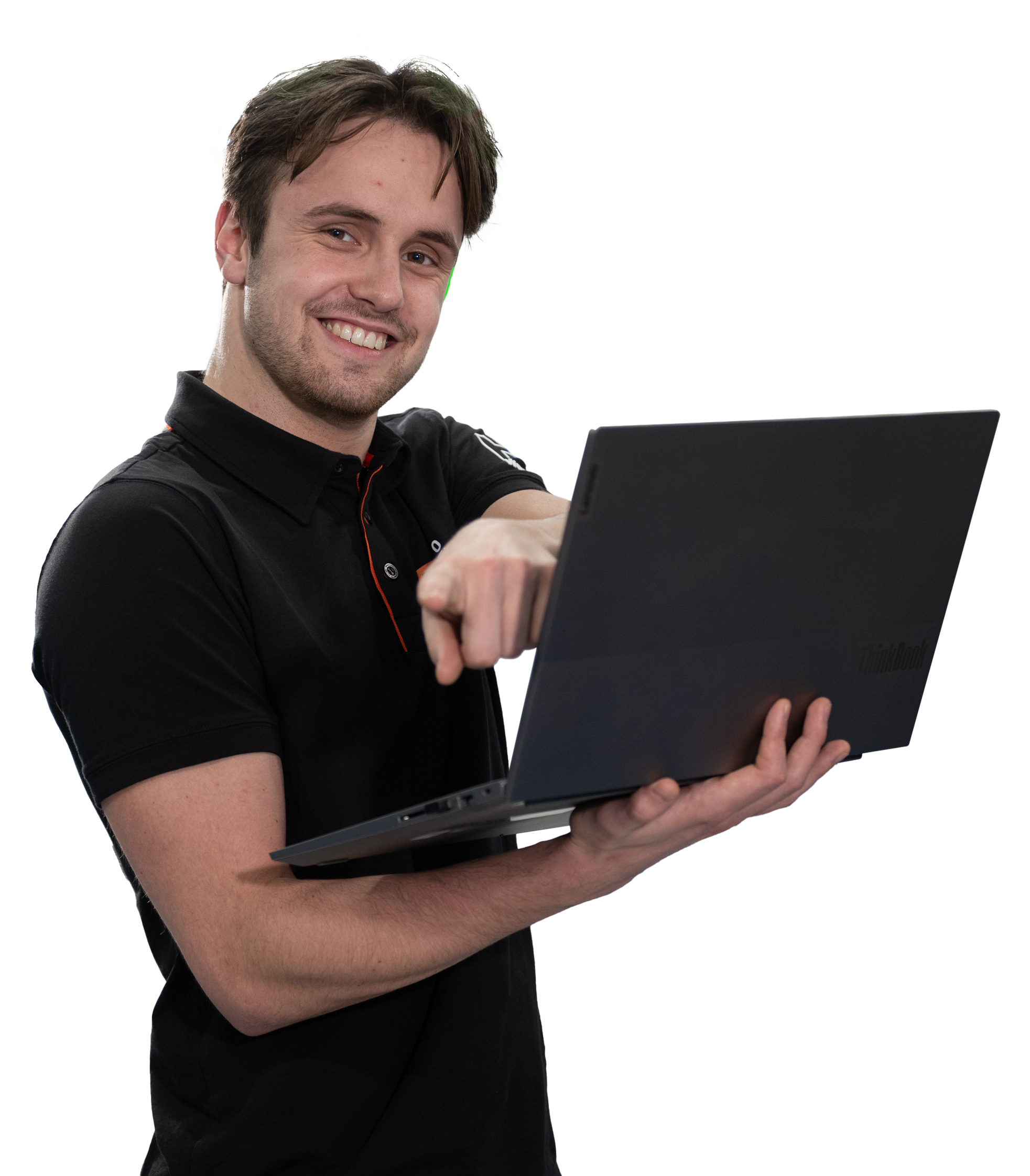
Ready to master your growth?
At AT-Automation, we aim to accelerate your growth and reach new heights of efficiency with our advanced automation solutions. We strongly believe in sharing knowledge and empowering individuals to become masters in industrial automation. Would you like free advice on how our solutions can help your business grow? Please leave your contact information below.
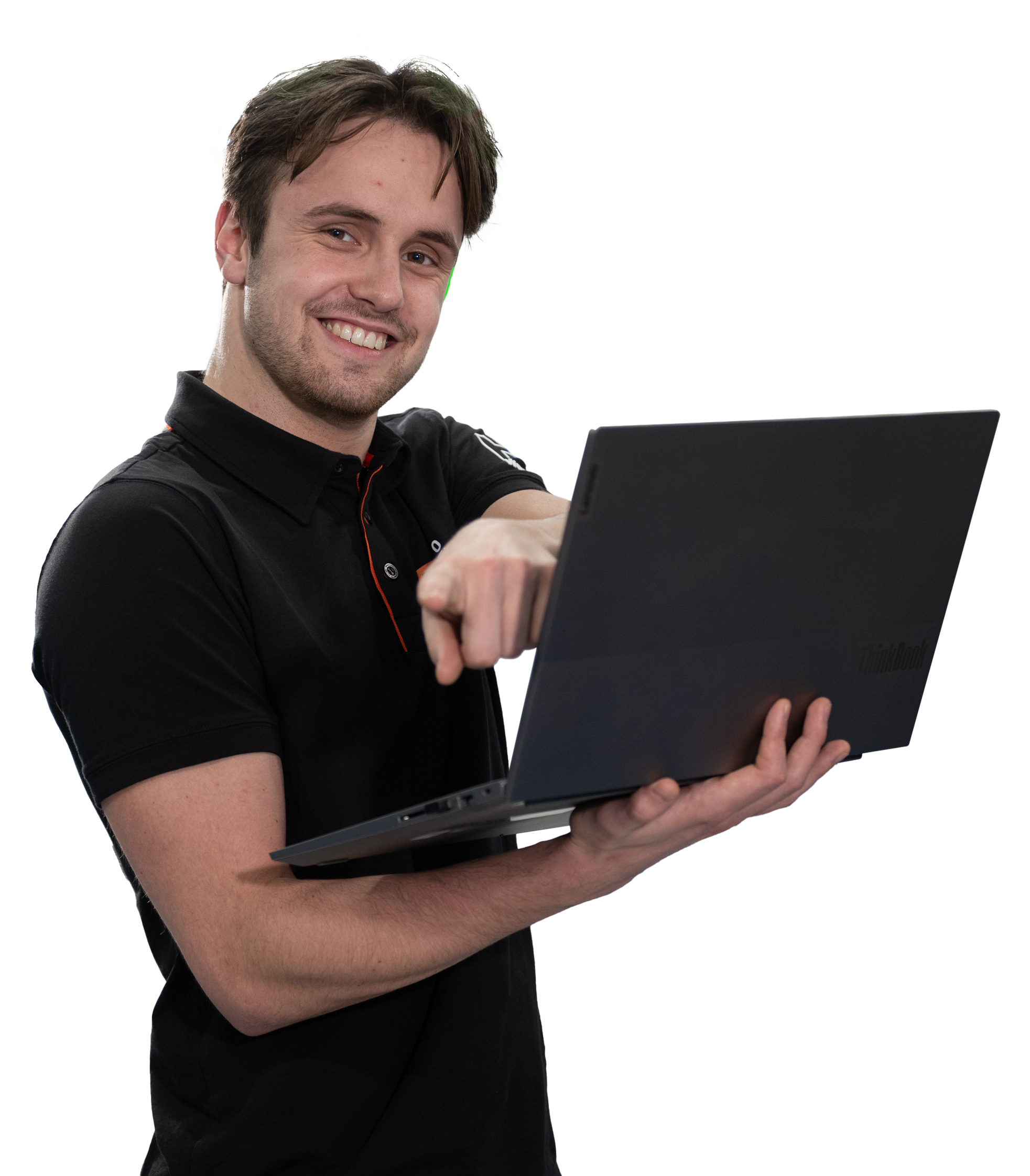