» What is SPC?
» How does it work?
» The history of SPC
» The benefits of SPC
» What are some common pitfalls when using SPC?
» Measure quality with Ignition
» Explore Ignition
Other knowledge base articles
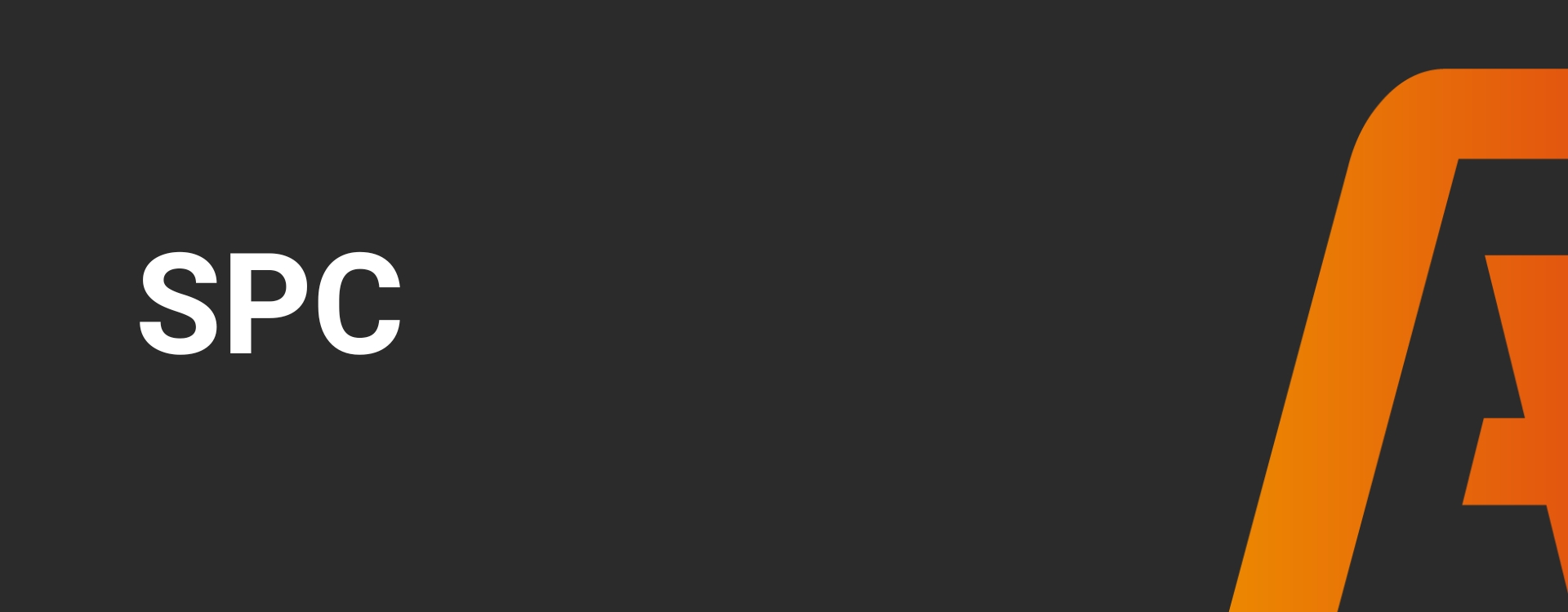
SPC
What is SPC?
SPC stands for Statistical Process Control. It is a method to measure and control quality by monitoring the production process. SPC collects and analyzes data to identify and manage variation in processes, thereby improving the quality of products and services and reducing costs.
It is commonly applied in the manufacturing industry, where it helps improve production line efficiency, minimize waste, and enhance product quality. However, it can also be used in other sectors such as healthcare and services to improve processes and achieve better outcomes.
The goal is to reduce variation in processes and keep them under control, so that the outcomes of the process are consistent and predictable. By monitoring and controlling a process with SPC, it operates at its full potential.
How does it work?
SPC is based on monitoring and analyzing data to understand and improve the performance of a process. Below are the basic steps of how SPC works:
- Identify the process you want to control and improve: This could be a manufacturing process, a service process, a logistics process, or any other business activity.
- Define the KPIs for the process: These are the measurable aspects of the process that are relevant to its quality and efficiency.
- Collect data: Regularly gather data on the process’s KPIs. This can be done manually or automatically, depending on the type of process.
- Analyze the data: Use statistical analysis to understand the variation in the data and determine if the process is under control. There are various statistical tools suitable for SPC, including control charts, histograms, and Pareto charts.
- Identify special causes of variation: If there are special causes of variation, such as machine faults, material issues, or operator errors, you need to identify and address them.
- Take corrective actions: Once special causes of variation are identified, take corrective actions to remedy them and ensure the process is back under control.
- Continue monitoring and improving: This is a continuous process. Keep collecting, analyzing, and improving data to enhance the quality and efficiency of the process.
The history of SPC
In the early twentieth century, Walter A. Shewhart, an American statistician, introduced the concept of statistical control charts. He developed this technique to manage variation in production processes and improve the quality of manufactured goods.
During World War II, this method was widely adopted by the military in ammunition and weapon factories. The demand for products forced them to seek a better and more efficient way to monitor product quality without compromising safety. SPC met that need.
The use of SPC techniques in America declined after the war. Subsequently, Japanese manufacturing companies began adopting it, where it is still widely used today. In the 1970s, it started to resurface as the American industry felt the pressure from high-quality imported products from Japan. Nowadays, it is once again a widely used quality tool in many industries worldwide.
The benefits of SPC
- Quality improvement: It helps identify sources of variation in production processes and provides insight into process performance, thereby enhancing product quality and reducing defects.
- Cost savings: By identifying and eliminating variation in the production process, this method helps reduce waste, optimize raw material usage, and decrease rework, resulting in significant cost savings for the company.
- Efficiency enhancement: Monitoring and controlling variation in production processes, SPC improves process efficiency and reduces waste.
- Customer satisfaction: By enhancing product quality and reducing defects, this method contributes to higher customer satisfaction.
- Proactive approach: This method enables proactive problem-solving and prevention rather than waiting for issues to arise and then taking action.
- Data-driven decision-making: Based on collecting and analyzing data on the production process, companies make decisions based on facts and data rather than intuition or assumptions.
- Process control: It assists in monitoring process performance, enabling companies to keep it under control and consistent, resulting in a more reliable production process and reducing the risk of downtime or failures.
- Continuous improvement: This method is part of the continuous improvement cycle and helps identify areas requiring improvement. By continuously monitoring and improving the process, the company builds a culture of improvement and adapts to changing conditions.
What are some common pitfalls when using SPC?
There are several common errors in using SPC. Below are some examples:
- Incorrect selection of process parameters: Choosing the wrong parameters leads to incorrect conclusions about the process and product quality.
- Lack of regular monitoring: Insufficient monitoring leads to unnoticed deviations and jeopardizes product quality.
- Lack of proper training and implementation programs: Inadequate employee training or poor implementation results in incorrect analyses and conclusions.
- Misinterpretation of SPC charts: Misinterpreting the charts leads to incorrect conclusions about the process and product quality.
- Excessive reaction to variability: Overreacting to minor process fluctuations results in unnecessary corrective actions and costs.
- Failure to follow up on corrective actions: Neglecting to follow up on corrective actions results in recurring problems and deviations.
Measure quality with Ignition
Ignition is a powerful industrial automation platform that combines HMI/SCADA, MES, and IIoT functionalities into one integrated solution. It utilizes various tools and technologies to collect and analyze data to monitor critical process parameters and improve process performance.
Ignition features built-in SPC capabilities such as generating control charts, performing calculations for process statistics, and providing alerts and notifications when process performance deviates from specifications.
The benefits of measuring SPC with Ignition:
- Integration: Ignition is an integrated platform that combines various functions including data acquisition, SCADA, MES, and SPC. This ensures seamless integration of SPC throughout the entire production process.
- Flexibility: Ignition offers a high degree of flexibility in configuring SPC functionalities. This allows for supporting and customizing the specific needs of different production processes.
- Real-time data: The software provides real-time data acquisition and analysis, enabling quick response to changes in the production process. This is essential for SPC as it allows for identifying and correcting process deviations before larger issues arise.
- Advanced analysis: Ignition offers a wide range of advanced analysis and reporting capabilities, including graphs, control charts, Pareto analyses, histograms, and more. These tools enable companies to conduct in-depth analysis and improve production process performance.
- Scalability: Ignition is scalable and adaptable to different production environments, from small production lines to large factories. This allows for implementing and expanding SPC as production grows.
Discover Ignition
your way
Start building
For developers
Get started with your own Ignition applications right away.
- Download and install Ignition easily and quickly.
- Explore all features.
- Connect unlimited tags, PLCs, databases, and devices.
Discover how Ignition solves your technical challenges without limitations.
See Ignition in action
For managers
Explore Ignition without any technical knowledge in the demo environment.
- No installation required.
- See how Ignition automates and visualizes processes.
- Adjust live values and see instant results.
Experience real-time automation and discover what it can offer your business.
Want to really know what Ignition can do for you?
Let us come to you for a free demo.
- Meet with our experts and ask all your questions.
- Get personalized advice.
- See how Ignition can optimize your processes.
The perfect opportunity to collaborate with specialists and see exactly how Ignition can help you achieve your business goals.
Start building your own application now!
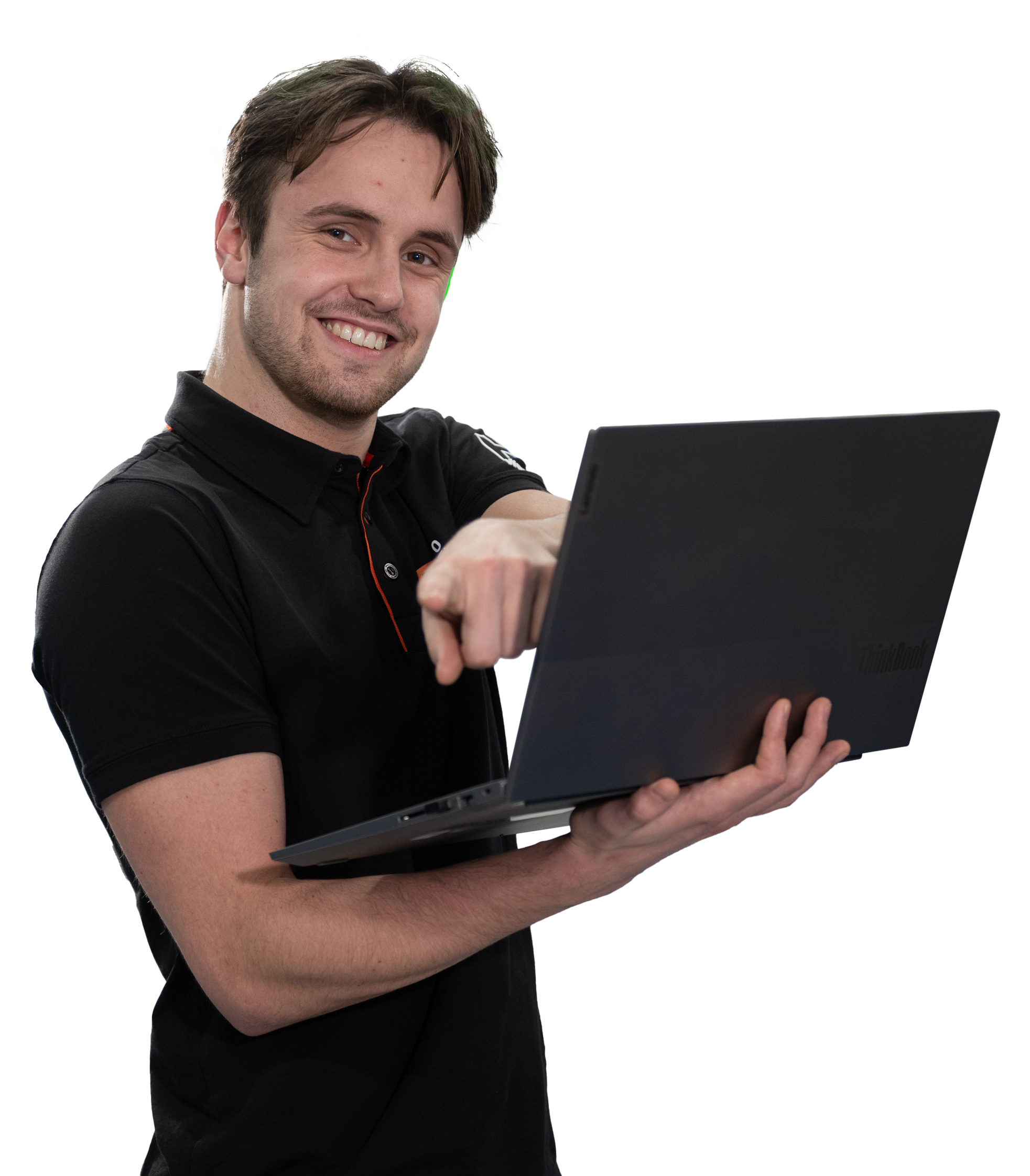
Discover how Ignition can improve your processes!
Want to see how Ignition automates and visualizes processes without any technical knowledge? Fill out the form and gain immediate access to the demo environment, where you can experience Ignition live.
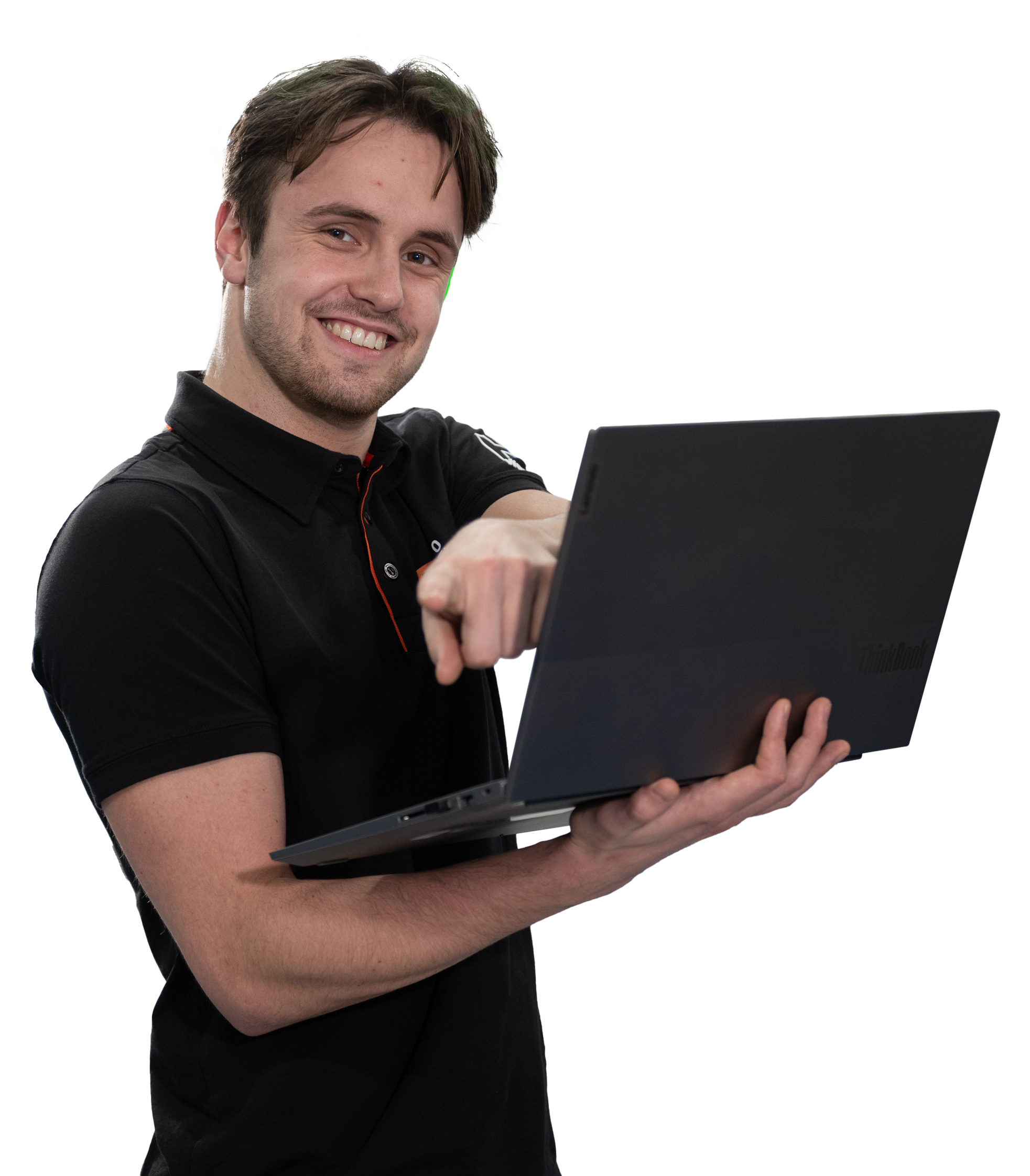
Schedule a no-obligation demo with our experts!
Want to learn more about how Ignition can optimize your processes? Request a personalized demo and discuss your business goals with our specialists. Fill out the form to book an appointment.
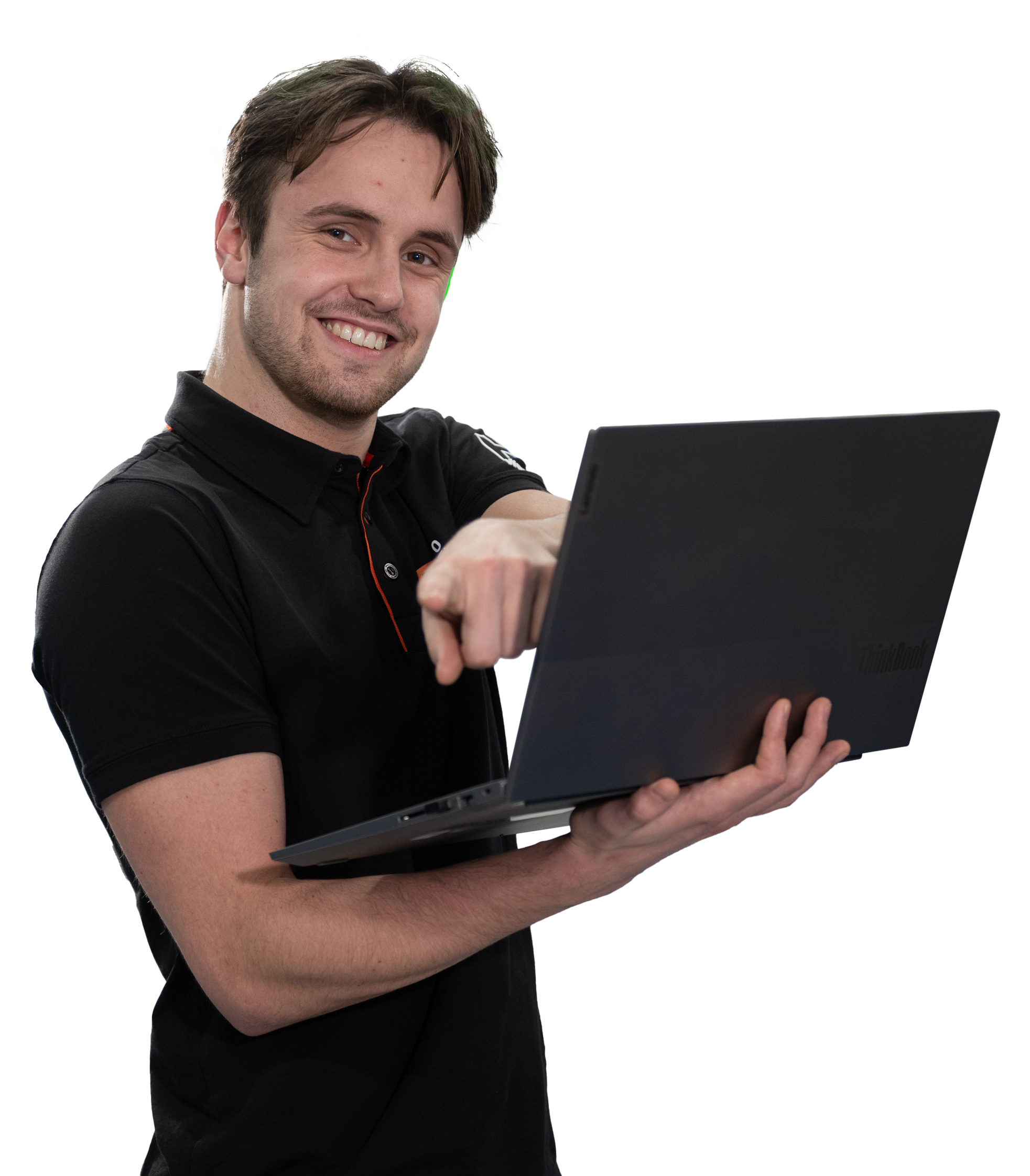