» What is industrial automation?
» How does industrial automation work?
» What are the benefits of industrial automation?
» What technologies are included in production automation?
» What are the trends in industrial automation?
» How does production automation contribute to sustainability?
» What are the challenges in implementing industrial automation?
» Industrial automation and Ignition
» Explore Ignition
Other knowledge base articles
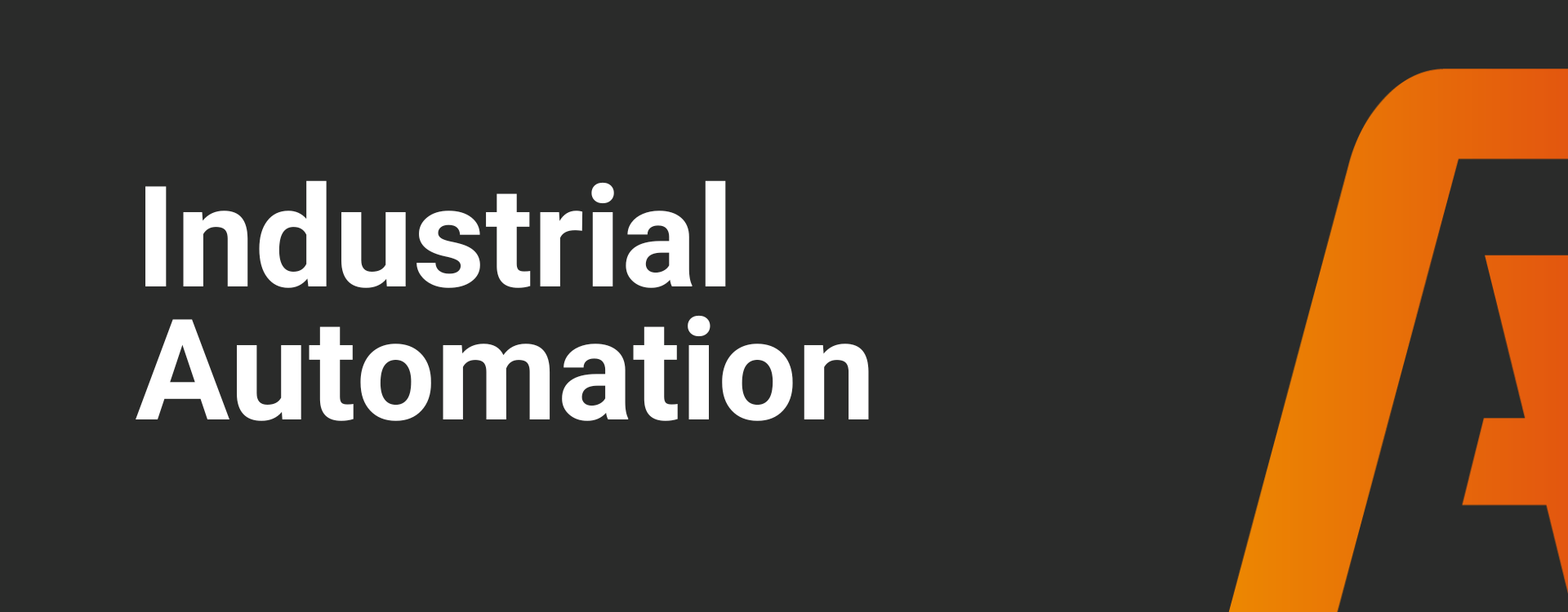
Production Automation
» What is industrial automation?
» How does industrial automation work?
» What are the benefits of industrial automation?
» What technologies are included in production automation?
» What are the trends in industrial automation?
» How does production automation contribute to sustainability?
» What are the challenges in implementing industrial automation?
» Industrial automation and Ignition
» Explore Ignition
What is industrial automation?
Industrial automation, also known as production automation, is the use of technologies and systems to automate and optimize production processes in the industry. This includes the use of machinery, computers, robots, sensors, and other equipment to control, monitor, and optimize production processes. The goal of industrial automation is to make production processes more efficient, safer, more reliable, and more sustainable. This is achieved by reducing errors and waste, improving product quality, increasing productivity, and reducing labor costs. Industrial automation is increasingly seen in various sectors, such as manufacturing, energy, chemistry, and transportation.
How does production automation work?
Production automation operates through a network of hardware and software that collaborate to automate production processes. Together, these components work to automate and optimize production processes. Sensors and actuators collect data about the production environment and send it to the PLC’s (Programmable Logic Controllers), which make decisions based on this data on how to control the machinery. The SCADA-software (Supervisory Control and Data Acquisition) provides operators with an overview of the entire system and enables them to quickly respond to any issues. The HMI’s (Human Machine Interfaces) allow operators to monitor and manage the system, as well as troubleshoot any problems. In this way, industrial automation makes production processes more efficient, safer, more reliable, and more sustainable.
What are the benefits of industrial automation?
- Increased efficiency: Makes production processes more efficient by reducing errors and waste, improving product quality, and reducing the time required to produce products.
- Increased safety: Reduces the risk of workplace accidents by reducing the amount of manual labor required to operate machinery and by improving safety measures in the production process.
- Reliability: Ensures consistent and reliable execution of production, improving quality and reducing the likelihood of malfunctions and downtime.
- Flexibility: Enables the configuration and modification of production processes to meet the changing demands of the market.
- Cost savings: Reduces labor costs by requiring less manual labor and also leads to more efficient use of raw materials and energy.
- Competitive advantage: Higher productivity, quality, and cost reduction provide a competitive advantage over companies that do not automate.
What technologies are included in production automation
Production automation utilizes a combination of hardware and software technologies to automate and optimize production processes, including:
- PLCs: Computer-controlled devices that use input from sensors and control the output of actuators. They are programmed to automatically perform actions based on predefined instructions.
- SCADA systems: Software platforms that collect, monitor, and analyze data from PLCs and other devices. They provide operators with an overview of the entire production process and enable them to quickly respond to any issues.
- HMIs: Screens and panels through which operators interact with the system. They enable operators to monitor and manage the system and troubleshoot any problems.
- Sensors and actuators: Devices that measure and control physical parameters such as temperature, pressure, position, and motion.
- Industrial networks: Networks specifically designed for industrial applications. They allow devices to exchange data and communicate with other devices in the system.
- Robots and machines: Physical devices that perform tasks such as assembling products or moving materials.
- IoT (Internet of Things): A technology that enables devices to communicate with each other and exchange data via the internet. This allows for remote monitoring and management of devices.
What are the trends in production automation?
There are several trends currently shaping the direction of production automation and are expected to further evolve in the future. Some of the key trends include:
Industry 4.0
Industry 4.0 involves the increasing integration of digital technologies and automation into production processes, aiming to create smart factories and achieve higher levels of flexibility, efficiency, and customization in manufacturing.
Collaborative robots (cobots)
Robots that collaborate with humans and are safe and flexible, making them suitable for various manufacturing environments. This provides more flexibility and safety in production processes.
Artificial intelligence (AI) and Machine Learning
AI and Machine Learning utilize smart algorithms and advanced analytics tools to optimize production processes, predict and prevent malfunctions, and enhance product quality.
Digital Twins
A digital replica of a physical object, such as machinery and production processes. This replica collects information on how the real object operates and uses this data to optimize it. This allows problems to be identified and resolved before they occur.
Cybersecurity
As industrial automation increasingly relies on digital technologies, cybersecurity becomes an increasingly important focus. Companies must ensure that their systems and processes are secure and protected against cyberattacks.
How does production automation contribute to sustainability?
Automated production processes contribute to a more efficient use of raw materials and materials, resulting in less waste. Additionally, the use of advanced automation systems optimizes energy consumption, leading to a reduction in energy consumption and thus CO2 emissions. Automated processes also help reduce the environmental impact of production by, for example, reducing emissions and waste production and minimizing the use of hazardous chemicals. Optimization of production processes through automation results in lower energy consumption and reduced waste production. Finally, companies are developing sustainable production methods using advanced automation technologies, such as the use of biodegradable materials or reducing the use of packaging materials.
What are the challenges in implementing industrial automation?
There are several challenges associated with the implementation of production automation, including:
- High initial costs: Such as acquiring new equipment and training personnel. This is particularly challenging for small and medium-sized enterprises.
- Integration with existing systems: This may be complex and requires careful planning and execution. It is also necessary to purchase new systems to ensure seamless integration.
- Complexity: Designing, developing, and implementing advanced automation systems can be complex, requiring a high level of expertise and experience to do so successfully.
- Safety: Automated systems pose safety risks, such as malfunctions or unforeseen events. It is important to implement safety procedures to mitigate these risks.
- Human factor: Automation leads to a reduction in employment and a change in the required skills of workers. It is important to provide adequate training and education for employees to keep up with the changes.
- Maintenance: Automated systems require maintenance to deliver optimal performance. It is important to have a good maintenance plan in place to prevent breakdowns.
Industrial automation and Ignition
Ignition is a software platform for industrial automation that offers a wide range of features for integrating, automating, and visualizing industrial processes. For example, the platform provides capabilities for data collection and analysis, HMI/SCADA, mobile access, reporting, and alarm management.
Industrial automation with Ignition offers a wide range of benefits, including improved productivity, increased efficiency, better quality control, reduced human errors, and decreased downtime. This is because the platform enables real-time data collection, process automation, and enhanced data visualization, providing operators and management with insight into what is happening in the factory or on the shop floor.
Furthermore, Ignition utilizes an open architecture, meaning it is easy to integrate with other systems and devices within industrial automation, such as PLCs, sensors, and motors. This allows businesses to integrate various systems and processes into one integrated and automated system.
In summary, industrial automation with Ignition helps streamline industrial processes, improve efficiency and productivity, reduce downtime, and provide real-time insight into what is happening on the shop floor.
Discover Ignition
your way
Start building
For developers
Get started with your own Ignition applications right away.
- Download and install Ignition easily and quickly.
- Explore all features.
- Connect unlimited tags, PLCs, databases, and devices.
Discover how Ignition solves your technical challenges without limitations.
See Ignition in action
For managers
Explore Ignition without any technical knowledge in the demo environment.
- No installation required.
- See how Ignition automates and visualizes processes.
- Adjust live values and see instant results.
Experience real-time automation and discover what it can offer your business.
Want to really know what Ignition can do for you?
Let us come to you for a free demo.
- Meet with our experts and ask all your questions.
- Get personalized advice.
- See how Ignition can optimize your processes.
The perfect opportunity to collaborate with specialists and see exactly how Ignition can help you achieve your business goals.