» What is an RTU?
» Who uses it?
» How does an RTU work?
» What types are there?
» What is the difference between an RTU and a PLC?
» What are the benefits of using an RTU?
» RTU and SCADA
» What is the lifespan of an RTU?
» Ready to master your growth?
Other knowledge base articles
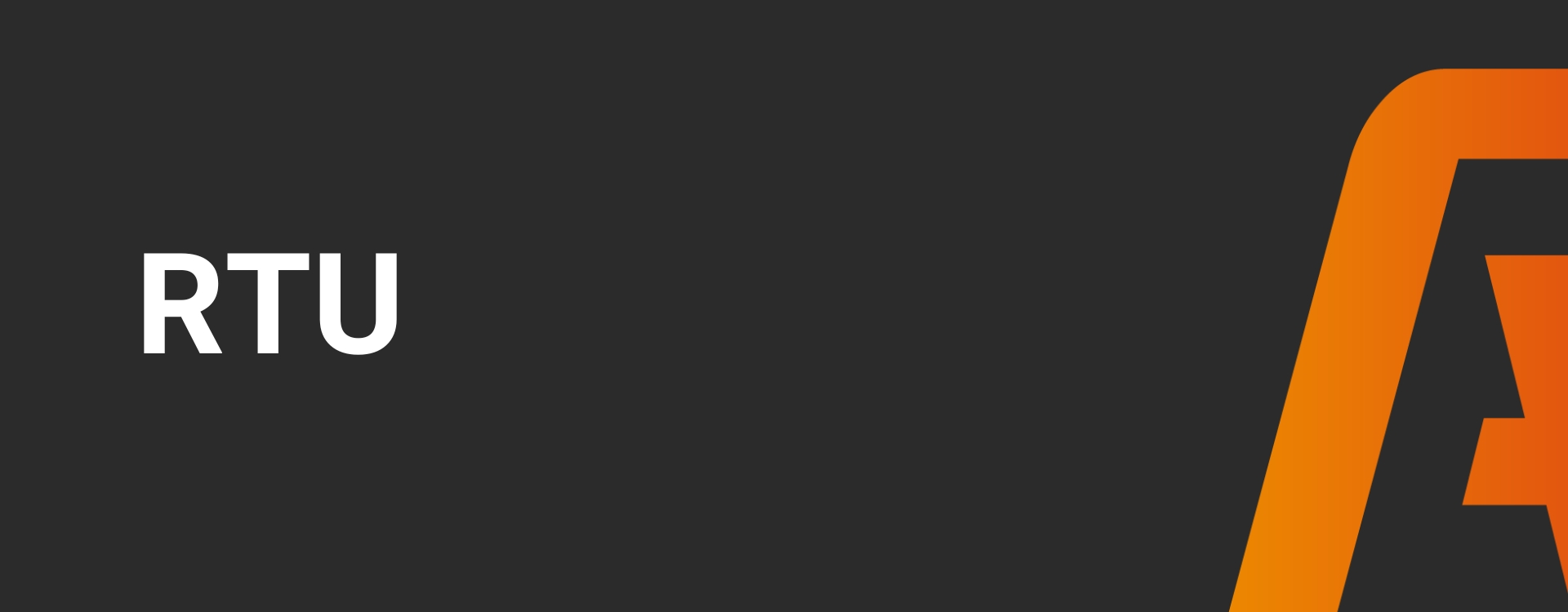
RTU
What is an RTU?
RTU stands for Remote Terminal Unit. This is an electronic device used in automated systems to collect data from sensors and devices in the field and transmit it to a central control system. It provides real-time control and monitoring of processes in the field. It is an important tool for automating and managing complex systems and improving operational efficiency and reliability.
Who uses it?
RTUs are primarily used in industrial and outdoor applications for data collection, control, and monitoring of automated processes and systems. A wide range of sectors and industries make use of them, including:
- Energy generation and distribution: for monitoring and controlling power plants, wind and solar energy installations, and electricity grids.
- Water management: in wastewater treatment plants, drinking water production and distribution, irrigation systems, and sewage treatment facilities.
- Oil and gas industry: for oil and gas extraction, transportation, and processing.
- Transportation: for monitoring and controlling signaling, traffic management, railway systems, and other transportation applications.
- Building management: to monitor and control the performance of building management systems.
How does an RTU work?
In most cases, they are connected to more advanced control systems, such as a computer. This makes reprogramming, monitoring, and managing the entire system easier. An RTU also monitors the analog and digital parameters of the production floor through sensors and data obtained from connected devices and systems. From here, the RTU sends data to the central control system.
An RTU contains setup software that connects the data input and output streams. The software defines protocols and even resolves installation issues. Depending on the manufacturer, purpose, and model, it can be expanded with various circuit cards. Due to their varying application possibilities, they come in many different hardware and software configurations and may even be completely incompatible with each other.
What types are there?
There are different types of RTUs, each with their own specifications and application areas. Below are some examples of the different types of RTUs:
- Standard: Used in industrial applications for data collection and remote process control.
- Intelligent: More advanced than standard RTUs, offering additional features such as data logging, programming, and more.
- Wireless: Deployed in environments where wiring is impractical, providing wireless communication and control capabilities.
- Embedded: Built into equipment such as pumps, motors, and sensors, offering control and monitoring of the equipment.
- Modular: Constructed in a modular fashion, allowing users to customize them to specific applications and requirements.
- Compact: Small and lightweight, often used in applications where space is limited.
- Low-power: Designed for applications where energy sources are limited, with low power consumption.
What is the difference between an RTU and a PLC?
An RTU is designed for applications in utilities, oil and gas industry, transportation, and other scenarios where data is typically collected and transmitted from sensors and devices in the field. The RTU serves as an interface between the field and the central control system. It gathers data from sensors and devices in the field, processes this data, and sends it to the central control system for processing and analysis. It also receives control commands from the central control system and forwards them to devices in the field.
PLCs (Programmable Logic Controllers), on the other hand, are commonly used for applications within a factory environment, aiming to monitor and automate the operation of machinery and processes. They collect data from sensors, process this data, and send commands to actuators and other devices in the field to control machinery and processes. They can also be used for automating logistical processes, such as moving goods within a factory.
What are the benefits of using an RTU?
- Real-time monitoring and control of devices in the field. This allows operators to immediately respond to issues and make quick decisions to improve system performance and efficiency.
- Efficient data collection from various types of sensors and devices in the field. This enables the assessment of system performance in an integrated and effective manner, leading to better operational decisions and helping operators to quickly resolve issues.
- RTUs are designed to be flexible and configurable for a wide range of applications. This makes them suitable for use in different sectors and applications, such as water management, energy generation, oil and gas industry, transportation, etc.
- They operate in harsh environments and are resistant to extreme temperatures, humidity, vibrations, and other environmental factors. The reliability and safety of the system are high, as they are equipped with security features to prevent unauthorized access to the system.
- Fewer operators are required because the system automatically collects data and executes control commands. This results in cost savings in terms of labor costs and improves system efficiency.
RTU and SCADA
Both are systems used for data collection, control, and monitoring in automated processes and applications. SCADA (Supervisory Control and Data Acquisition) is a software package used for visualizing, controlling, and monitoring automated processes and systems. It utilizes data collected by RTUs and other devices to provide real-time information about the performance and efficiency of the system to operators in a control room or central control panel. SCADA is used to set alarms, perform analyses, generate reports, and other tasks to optimize system performance.
In fact, these systems often work together in automated processes. The RTU collects data from sensors and devices in the field and transmits it to the SCADA system. The SCADA system processes and analyzes the data and provides real-time information to operators in a control room or central control panel. This enables operators to quickly resolve issues, improve system efficiency, and optimize performance.
What is the lifespan of an RTU?
The lifespan depends on various factors such as the quality of the device, environmental conditions, and how it is used and maintained. Generally, they have a lifespan of at least 10 to 15 years. Some may last longer than that, while others may need replacement earlier.
It is important to perform regular maintenance to ensure they continue to function properly. This may include cleaning the housing, checking the wiring, and replacing outdated components. Timely maintenance and replacement of parts can extend the lifespan and ensure the reliability of the equipment.
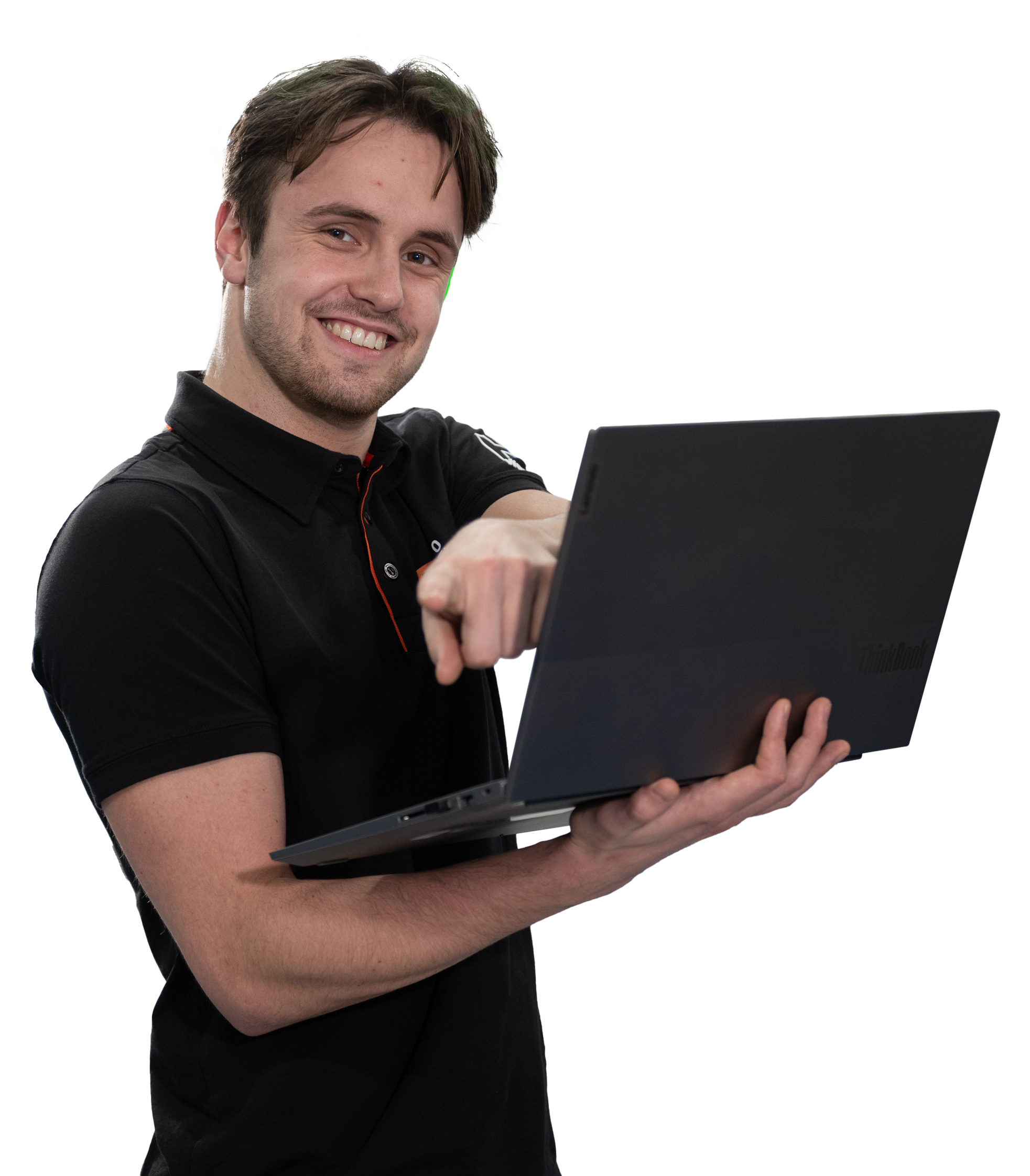
Ready to master your growth?
At AT-Automation, we aim to accelerate your growth and reach new heights of efficiency with our advanced automation solutions. We strongly believe in sharing knowledge and empowering individuals to become masters in industrial automation. Would you like free advice on how our solutions can help your business grow? Please leave your contact information below.
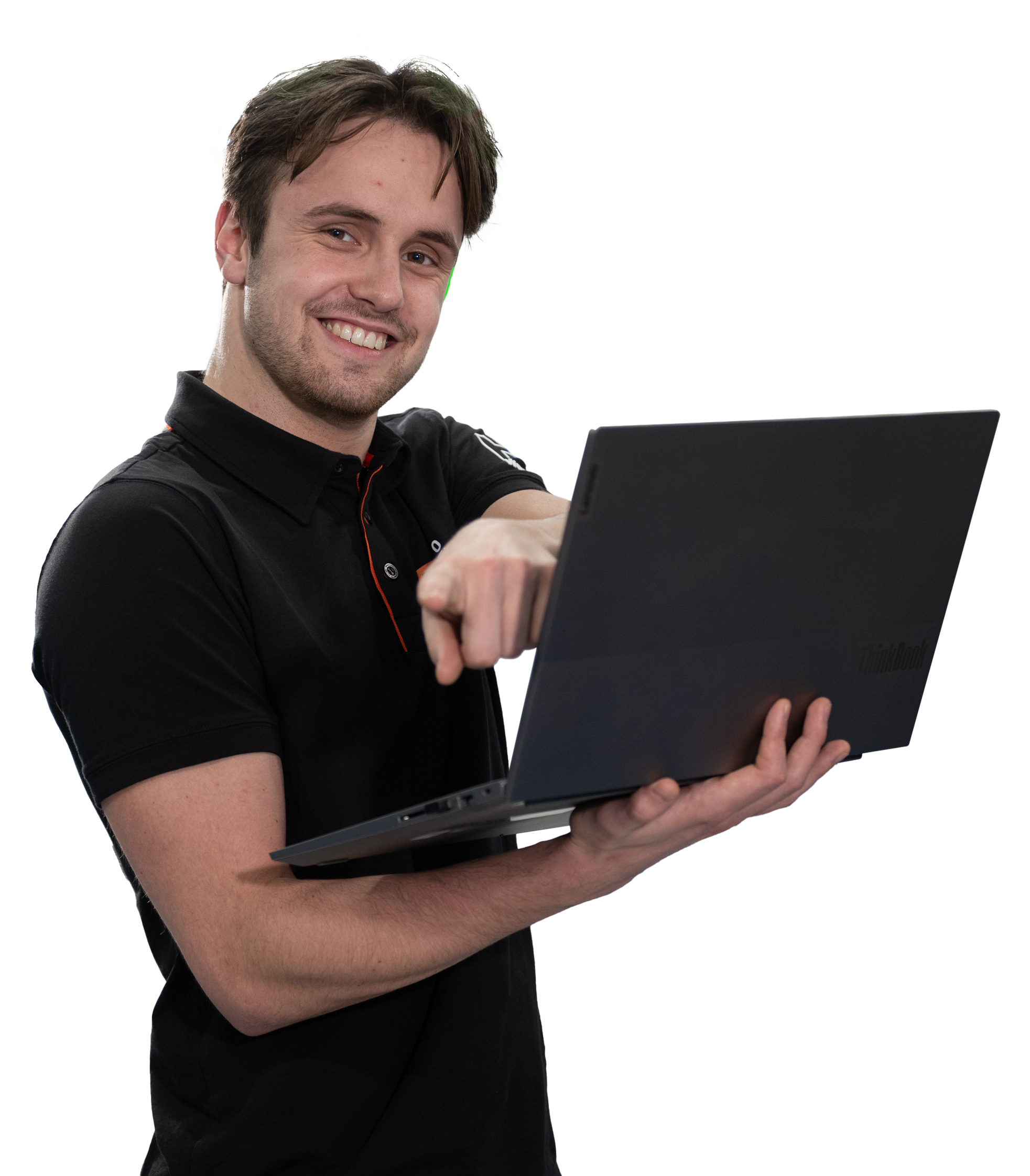