» What is a SCADA system?
» How does a SCADA system work?
» What are the key components of a SCADA system?
» Who uses SCADA?
» What are the benefits of SCADA?
» The origin of SCADA
» Modern SCADA systems
» Ignition: The new SCADA
» Explore Ignition
Other knowledge base articles
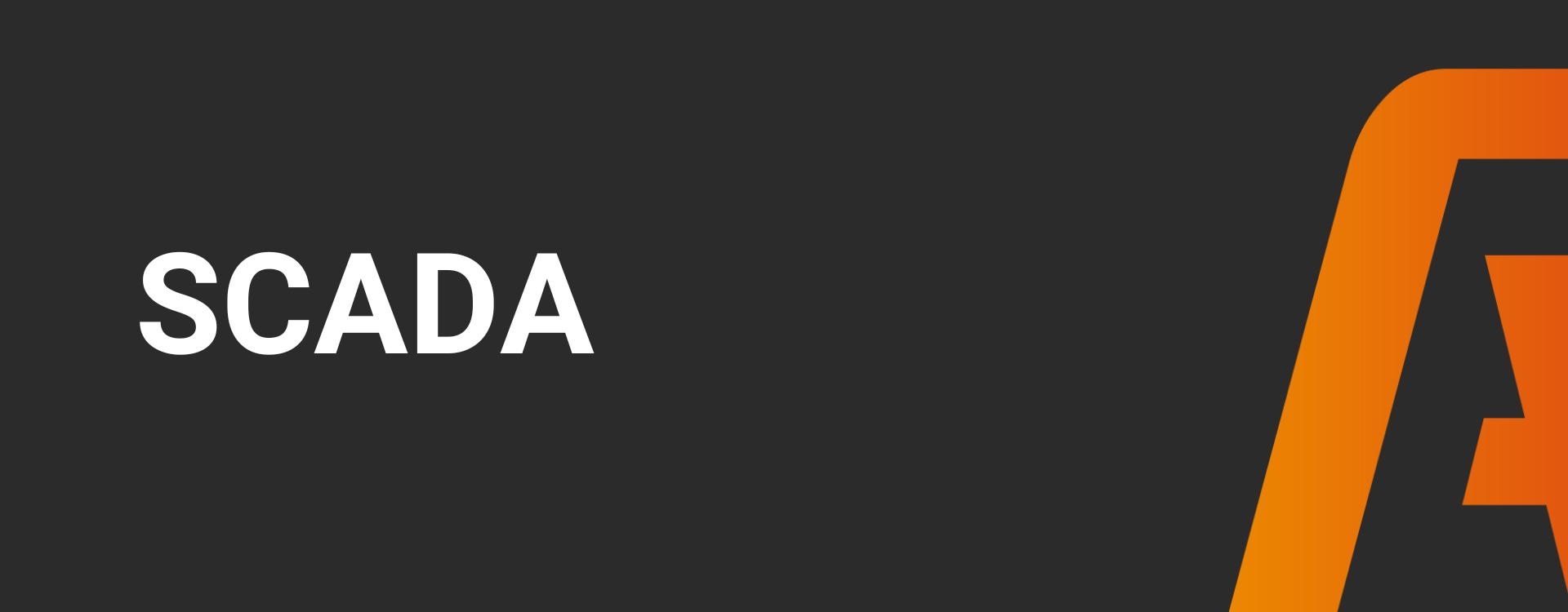
SCADA
What is a SCADA system?
SCADA stands for Supervisory Control and Data Acquisition. It is a system of software and hardware elements that enable industrial organizations to:
- Control industrial processes both locally and remotely
- Have direct interaction with devices such as sensors, valves, pumps, motors, and more via HMI software
- Monitor, collect, and process real-time data
- Capture events in a log file
A SCADA system is crucial for industrial organizations. They help maintain efficiency, process data for smarter decisions, and communicate system issues to minimize downtime. These systems are used to monitor and control a wide range of process variables such as temperature, flow rate, pressure, and level. Additionally, they enable process automation, leading to increased efficiency, lower labor costs, and enhanced safety.
How does a SCADA system work?
De basic architecture starts with PLCs (Programmable Logic Controllers) or RTUs (Remote Terminal Units). These are microcomputers that communicate with factory machines, HMIs, sensors, and devices, and then forward the data retrieved from these objects to computers running SCADA software. The software processes, distributes, and displays the data, allowing operators and other personnel to analyze the data and make important decisions.
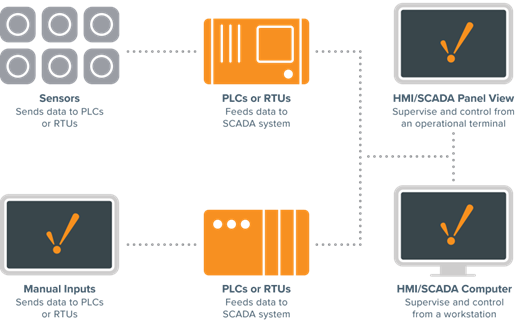
The system alerts an operator when a batch of product exhibits numerous errors. The operator pauses production and reviews the system data via an HMI to determine the cause of the issue. The operator reviews the data and discovers that machine 4 experienced a malfunction. The system’s ability to notify the operator of a problem helps him resolve the issue quickly and prevent further production loss.
What are the key components of a SCADA system?
- RTUs: Devices located at various points in the process or facility. They collect data from field equipment, such as sensors and actuators, and send it back to the central computer for analysis. RTUs also receive commands from the central computer and use them to control the process or equipment.
- PLCs: Specialized computers designed to control industrial processes. They are often used in conjunction with RTUs to provide more advanced control capabilities.
- Central computer or server: Acts as the central point for collecting and analyzing data. It receives data from the RTUs and PLCs and processes it for display on operator workstations. It also sends commands to the RTUs and PLCs to control the process or equipment.
- Operator Workstations: Devices (computers, tablets, and mobile phones) used by operators to view and control the process or equipment. They are typically connected to the central computer and display process data, alarms, and other information.
- Communication network: Connects all components of the SCADA system together. It may include various technologies such as wired or wireless networks, depending on the specific application.
- HMI: The interface used by operators to interact with the SCADA system. It is used to display process data, control the process, and acknowledge alarms.
- Data logging: The system stores all data in a database for use in reporting and trend analysis.
- Alarm and event management: The system generates alarms and events when certain conditions are met. For example, when a sensor reading exceeds a certain threshold. This allows operators to quickly identify potential issues and respond accordingly.
Who uses SCADA?
SCADA systems are used by industrial organizations and companies in the public and private sectors to monitor and maintain efficiency, distribute data for smarter decisions, and communicate system issues to help minimize downtime. These systems work well in many different types of enterprises because they range from simple configurations to large, complex installations. They form the backbone of many modern industries, including:
- Energy
- Food and beverage
- Manufacturing
- Oil and gas
- Recycling
- Transportation
- Water and wastewater
- And much more
Virtually everywhere in today’s world, some SCADA system is working behind the scenes. Think of maintaining the cooling systems in the local supermarket, ensuring production and safety in a refinery, achieving quality standards in a wastewater treatment plant, or even tracking your energy consumption at home. Effective systems deliver significant savings in both time and money.
What are the benefits of SCADA?
- Remote monitoring and control: Operators are able to remotely monitor and control industrial processes from a central location. This enhances efficiency and reduces the need for on-site personnel.
- Real-time data collection: SCADA systems collect data in real-time, which is then used to optimize processes and make real-time decisions.
- Automation: Certain processes, such as device activation and deactivation, can be automated. This improves efficiency and reduces the risk of human error.
- Alarm and event management: Alarms and events are automatically generated when certain conditions are met, such as when a sensor reading exceeds a certain threshold. This enables operators to quickly respond to potential issues.
- Historical data logging: These systems store historical data, which is then used for analysis, trending, and reporting.
- Enhanced safety and security: SCADA enhances safety by allowing operators to monitor and control processes from a secure location, reducing the need for personnel in potentially hazardous areas. Additionally, security measures can be implemented to protect the system from unauthorized access.
- Cost savings: By improving efficiency, reducing the need for on-site personnel, and automating certain processes, a SCADA system reduces costs.
The origin of SCADA
To understand the origin of SCADA, we need to grasp the challenges that industrial organizations were trying to address. Before SCADA was introduced in the mid-20th century, many manufacturing plants, industrial factories, and remote locations relied on personnel to manually operate and monitor equipment via push buttons and analog dials.
As industrial floors and remote sites grew larger, solutions were needed to control equipment over long distances. Industrial organizations began using relays and timers to provide some level of supervision without the need to send people to remote locations to operate each device.
While relays and timers solved many problems by providing limited automation functionality, more issues arose as organizations expanded further. Relays and timers were difficult to reconfigure and troubleshoot, and control panels took up racks full of space. There was a need for a more efficient and fully automated control and monitoring system.
In the early 1950s, computers were first developed and used for industrial control purposes. Supervisory control became popular at that time among major utility companies, oil and gas pipelines, and other industrial markets. In the 1960s, telemetry was introduced for monitoring, enabling automated communication to transmit measurements and other data from remote locations to monitoring equipment. The term “SCADA” was coined in the early 1970s, and the emergence of microprocessors and PLCs in that decade enhanced enterprises’ ability to monitor and control automated processes more than ever before.
Modern SCADA systems
With modern SCADA systems, real-time data from the factory floor is accessible anywhere in the world. Thanks to this access to real-time information, governments, businesses, and individuals can make data-driven decisions on how to improve their processes. Without this software, it would be extremely difficult, if not impossible, to gather enough data for consistently well-informed decisions.
Furthermore, most modern SCADA packages have Rapid Application Development (RAD) capabilities. This allows users to relatively easily design applications, even if they don’t have extensive knowledge of software development.
The adoption of modern IT standards and practices such as SQL (Structured Query Language) and web-based applications in SCADA software has greatly improved the efficiency, security, productivity, and reliability of SCADA systems.
SCADA software that utilizes SQL databases offers enormous advantages over outdated SCADA software. One significant benefit of using SQL databases with a SCADA system is that it is easier to integrate into existing MES and ERP systems, allowing data to flow seamlessly throughout an entire organization.
Historical data from a SCADA system can also be stored in a SQL database, making data analysis through data trends easier.
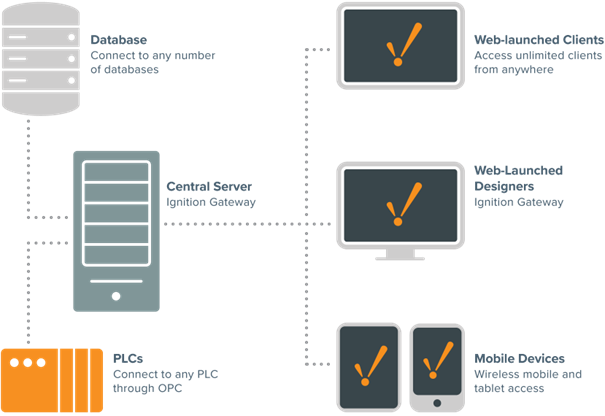
Ignition: The new SCADA
Ignition is an industrial automation software platform that many companies and organizations have switched to for their HMI/SCADA needs. Since 2010, Ignition has been installed at thousands of locations in over 100 countries. Its powerful and robust nature allows us as Ignition Integrators to meet the demands of our customers while costing less than other SCADA software solutions.
Here are a few reasons why more companies are choosing Ignition:
- Ignition uses modern IT practices, making it compatible with current SCADA system components.
- The unique licensing model allows users to pay a fixed amount based on the number of servers. Other vendors usually charge per user or per tag, but Ignition offers an unlimited number of users and tags.
- Ignition is web-deployable: it can be downloaded and installed in just a few minutes, and users can start or update it instantly.
Discover Ignition
your way
Start building
For developers
Get started with your own Ignition applications right away.
- Download and install Ignition easily and quickly.
- Explore all features.
- Connect unlimited tags, PLCs, databases, and devices.
Discover how Ignition solves your technical challenges without limitations.
See Ignition in action
For managers
Explore Ignition without any technical knowledge in the demo environment.
- No installation required.
- See how Ignition automates and visualizes processes.
- Adjust live values and see instant results.
Experience real-time automation and discover what it can offer your business.
Want to really know what Ignition can do for you?
Let us come to you for a free demo.
- Meet with our experts and ask all your questions.
- Get personalized advice.
- See how Ignition can optimize your processes.
The perfect opportunity to collaborate with specialists and see exactly how Ignition can help you achieve your business goals.