One source of truth for all departments
Category: SCADA, MES & IIoT | Customer: EKK Eagle Simrax
Project Scope
- Tags: 20,181
- Screens: 69 Perspective pages
- Users: 30 continually active, several occasionally
- Alarms: 447, with future increases
- Devices: 37 Mitsubishi PLCs, 1 Siemens PLC, SAP, Logitime
- Architectures: Standard
- Databases: 1 Microsoft SQL Server Cluster
- Historical data: 5,491 tags, with additional manual logging, 28,000,000 rows per week
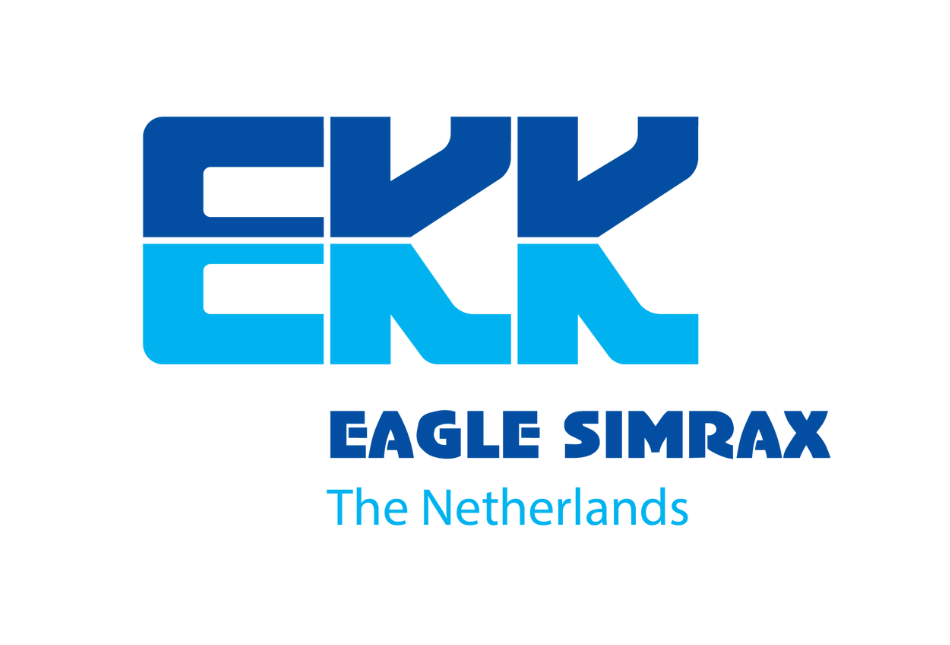
Project Overview
Ignition was deployed to develop a SCADA/MES application for EKK Eagle Simrax that replaces numerous separate Excel sheets and an outdated Citect SCADA platform. By leveraging Ignition, AT-Automation created a single source of truth for all departments within the company (production, process engineering, technical services, quality, logistics).
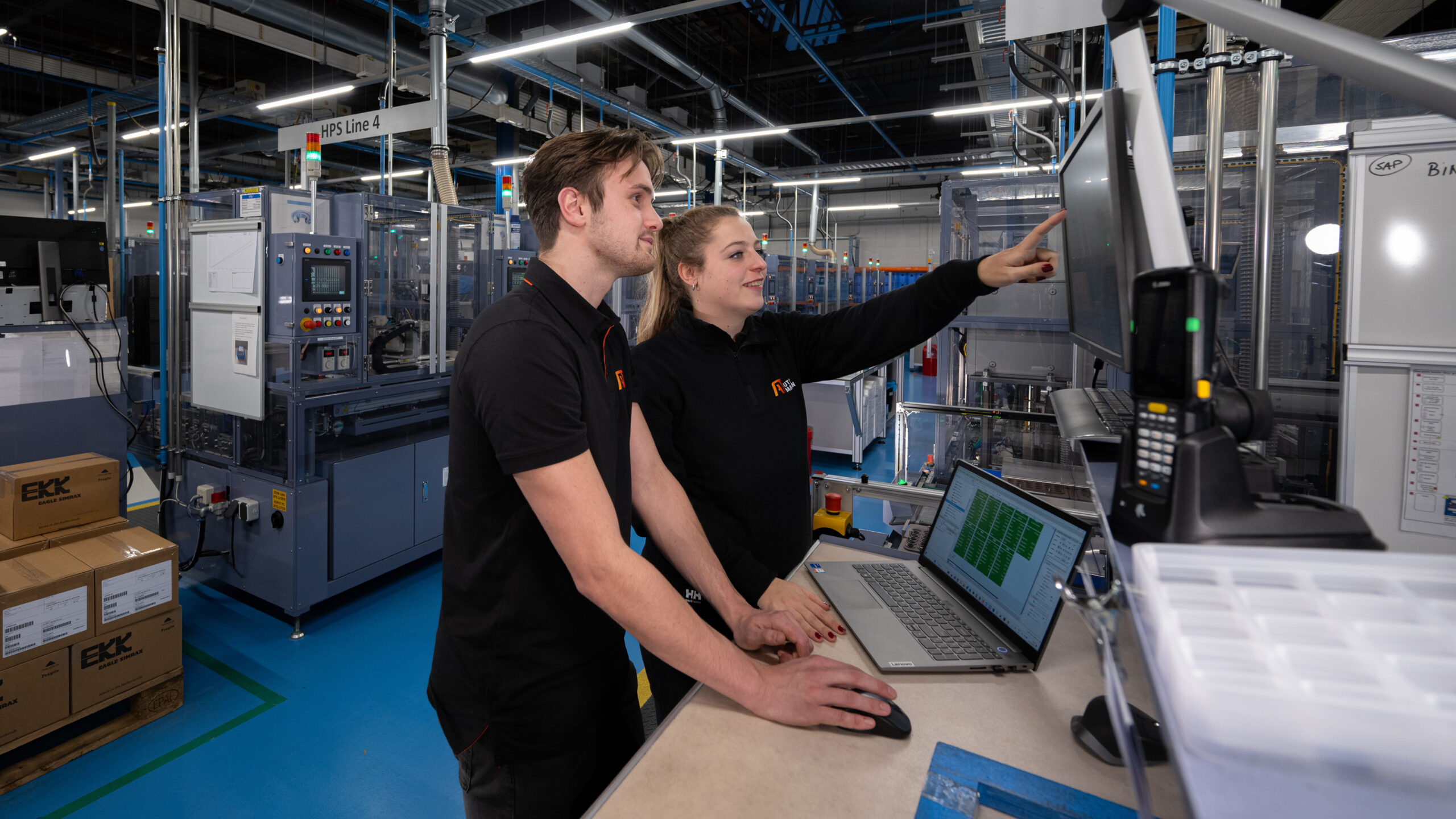
Problem
EKK Eagle Simrax is a Dutch company that produces more than 30 million seals annually for the automotive sector. As a market leader in precision production, they promise high quality to their customers by inspecting every manufactured part.
With a desire to continuously improve their processes, EKK Eagle Simrax decided to replace their existing SCADA system, Citect. Previously, data was recorded and analyzed using Excel sheets managed separately by each department. This led to inefficiencies and confusion during improvement discussions. The introduction of Ignition now provides a standardized way to present data, saving time by automating and standardizing nearly all reports. improve. With Ignition, they have created one unambiguous way of presenting the data, and are able to save time since almost all the reports are automated and standardized.
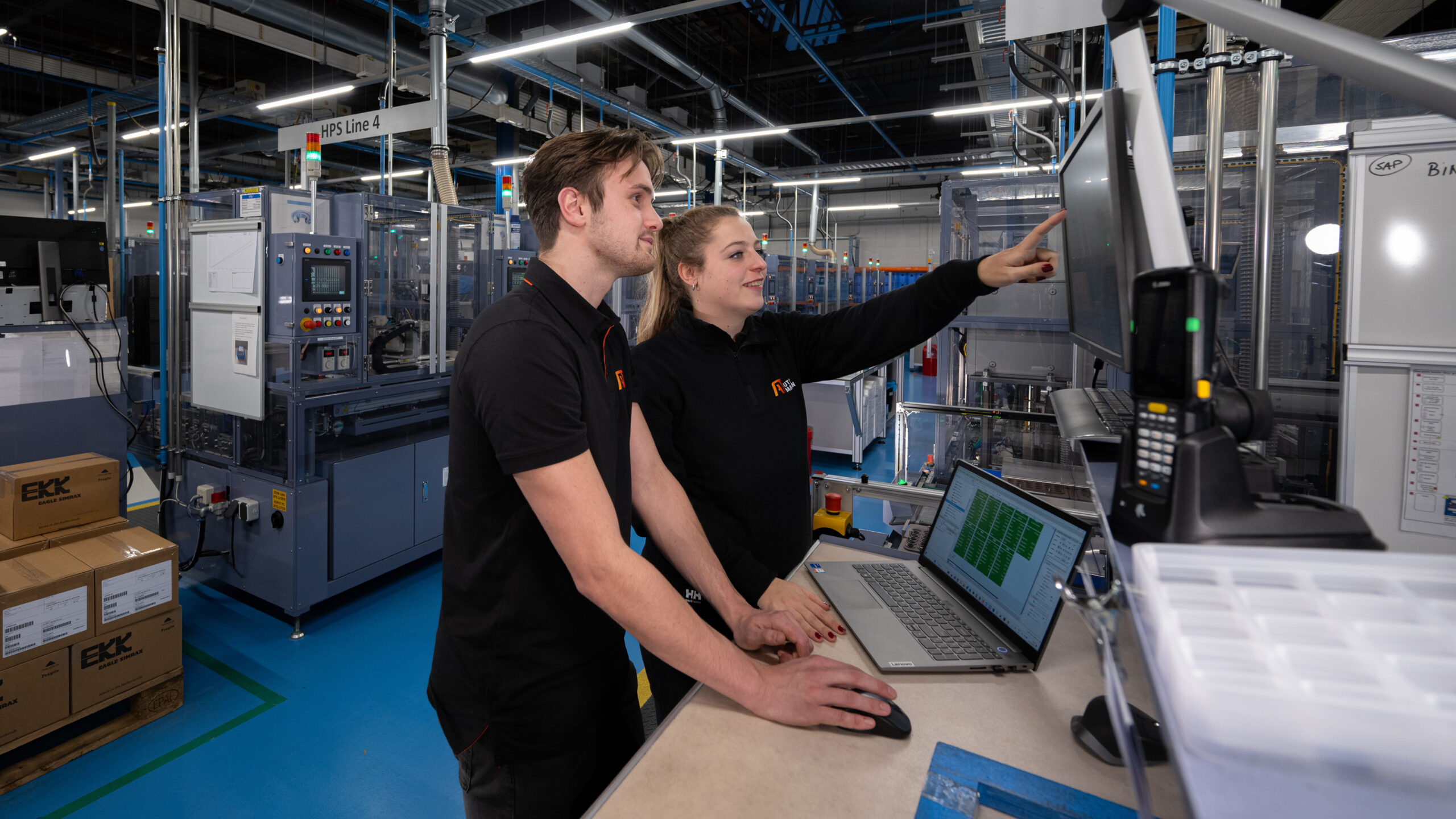
“Previously, we were compelled to approach the integrator for every minor adjustment. The foundation of Ignition is easy to understand and set up, enabling our engineers to make these adjustments themselves.”
Sam Helsens, EKK Eagle Simrax
Solution
Ignition was used to create a SCADA/MES solution accessible via browser (Perspective unlimited), allowing everyone in the company to use personal dashboards. Navigation is dynamically built based on roles (10+ possibilities). The various dashboards are generated from the same data, providing a consistent overview of the production process. EKK Eagle Simrax aims to improve processes and minimize downtime for all production lines. Downtime registration is done automatically based on PLC tags, with data viewable as raw datasets or in pie/bar charts.
Additionally, AT-Automation established connections with SAP (ERP system) and Logitime (time registration program) for data exchange between these systems. The SAP integration retrieves orders. The next project upgrade will include planning these orders and creating a live dashboard of order progress, including downtime, changeover time, and process speed loss. The connection also logs production waste.
AT-Automation also developed SCADA screens for operators to view live production data and historical trend data. Trends can be saved for later use or shared within the company. All SCADA screens are dynamically built but can function without a database connection. High-level overview screens were also created to give managers a quick snapshot of current production status without navigating multiple screens.
Result
Ignition is now used for all activities related to production numbers, quality control, and process improvements. The application is utilized by everyone in the company, from operators to executives. Instead of multiple systems and Excel sheets, there is now one application handling all tasks.
This consolidation has resulted in a satisfied customer who wants Ignition to play an even more prominent role in their production process. Integrating all functionalities into one project has eliminated waiting times when switching between systems. Future expansions will include track & trace, order planning, and inventory management.
The old SCADA system had issues with data processing; for example, it could only save one data point every four minutes, which now happens every second. Additionally, the old SCADA system took over six minutes at the end of each shift to process data and send it to SAP. This now occurs in the background, providing an additional 18 minutes of production per line daily. With 35 lines, that’s 10.5 hours of extra production per day!
EKK Eagle Simrax now controls their software, enabling them to adjust reports and screens and save costs by not needing integrators for every minor change. Since implementing Ignition, paper has become obsolete in the production environment, as all data can be directly recorded in Ignition.
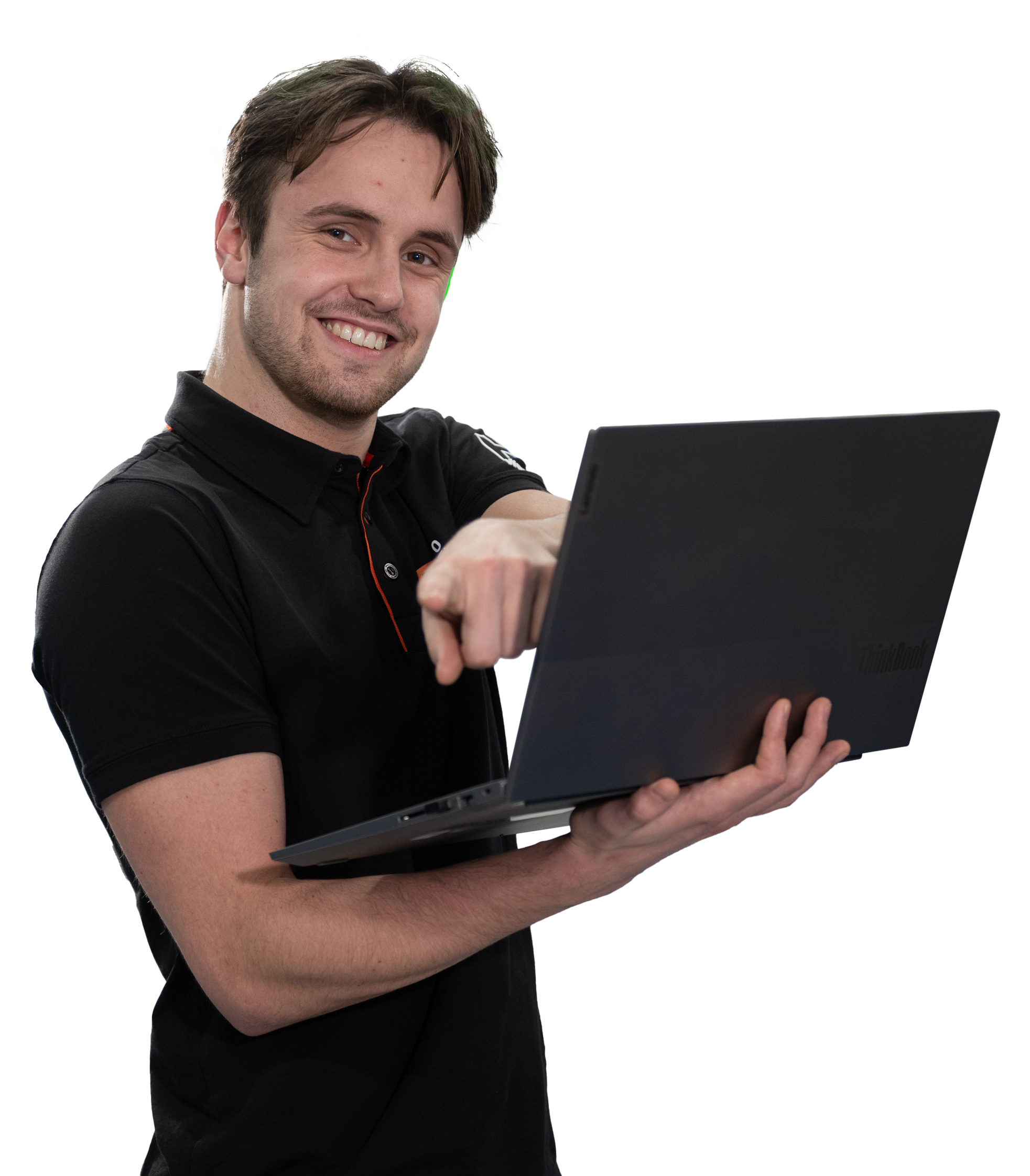
Ready to master your growth?
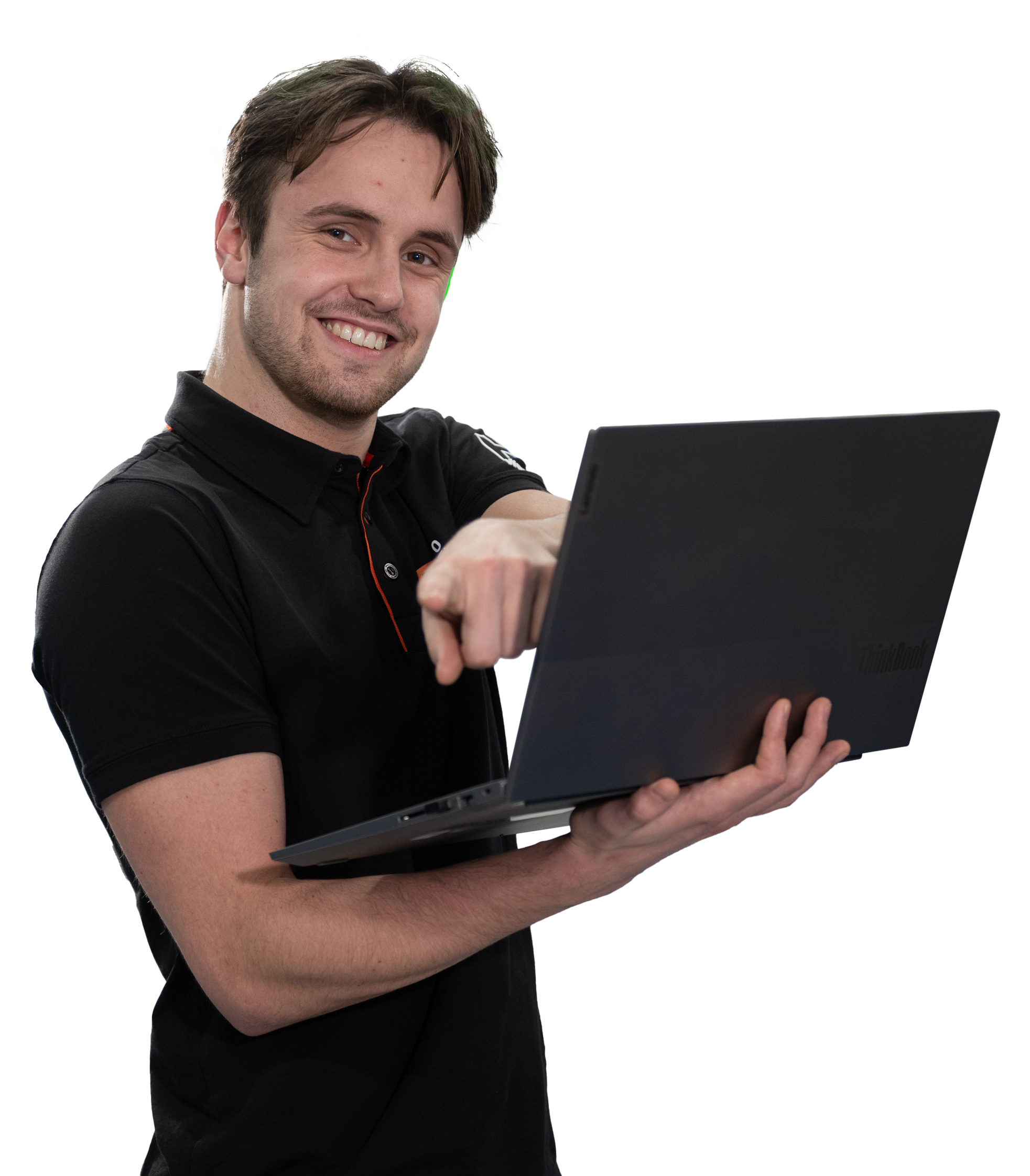